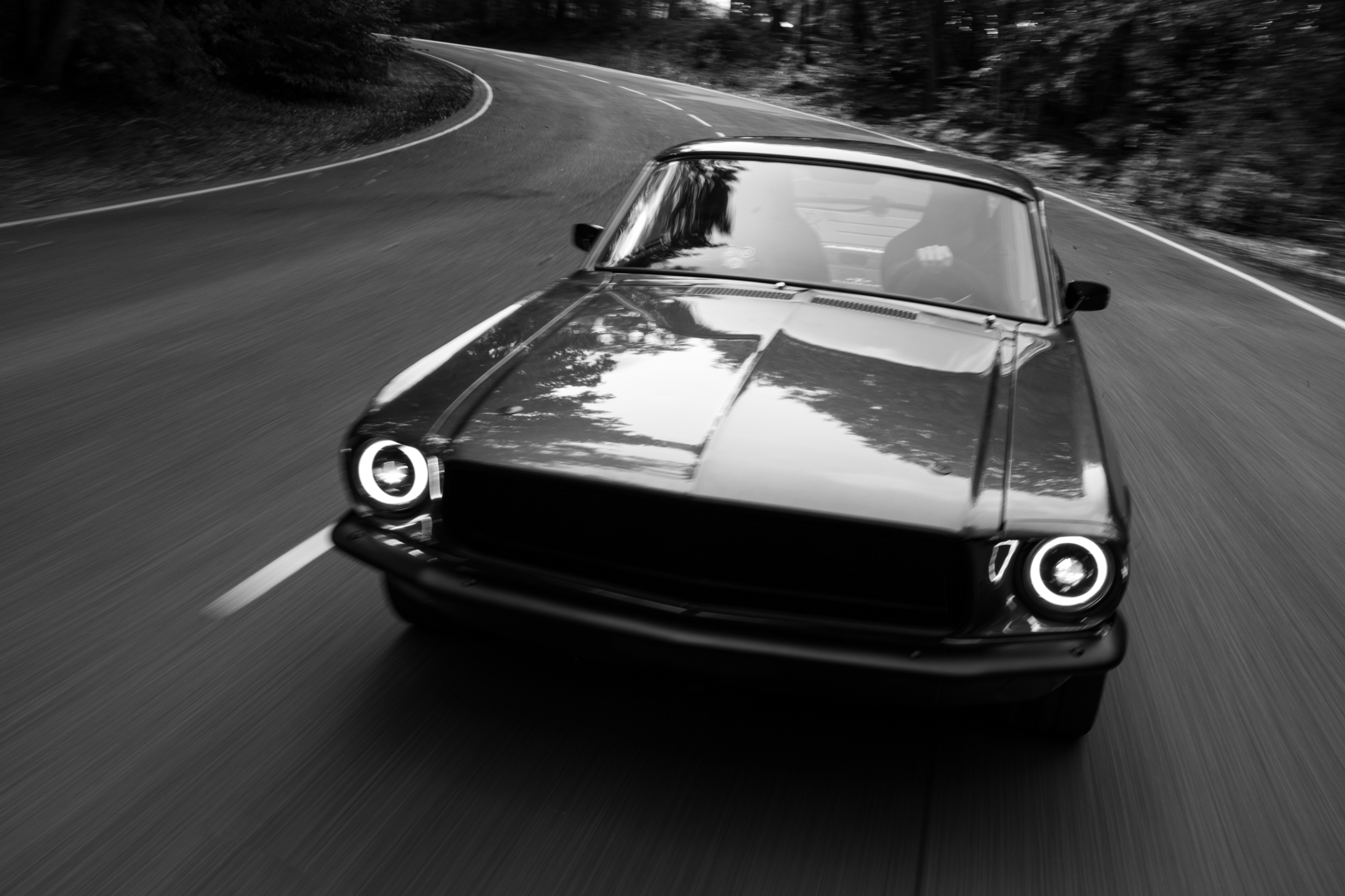
Charge Cars
Photographs taken at an EV start-up whilst working as a Design Engineer
Documentary, Commercial, Street, Product.
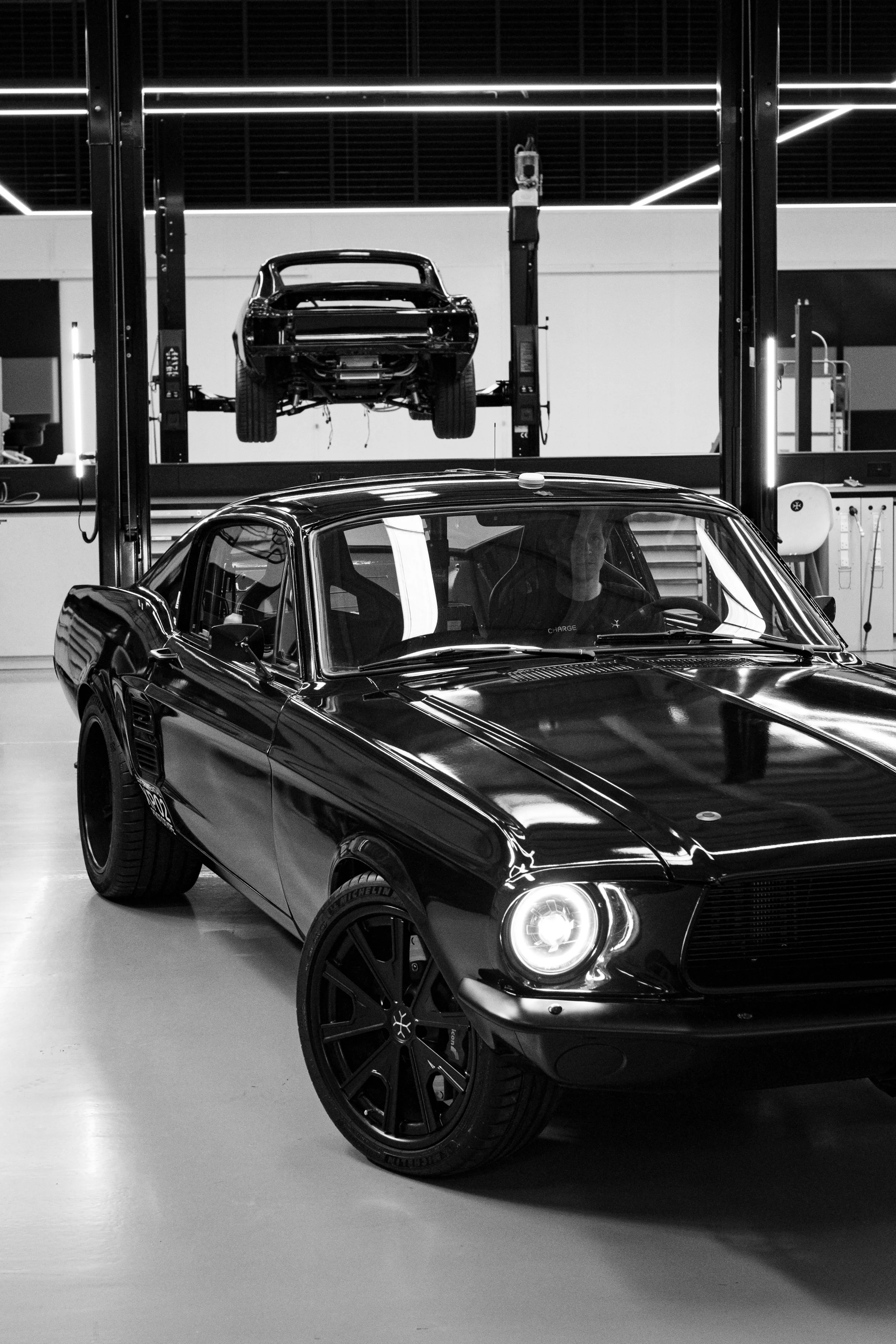

I made time for photographing the Charge Car journey, for future use in marketing and social media alongside contributing on various design and engineering projects.
When the Creative Director saw the pictures I was capturing, I was quickly enlisted as the resident photographer to document Charge Cars' story. I continued to capture important milestones and candid moments of talented minds collaborating to engineer, manufacture and actualise a dream.
This gallery of select images, accompanied by insightful comments, documents the Charge Car heritage.
A tech start-up designing an all-electric ‘67 Mustang
Using the original tooling, licensed by Ford, Charge Cars are producing new metal Mustang chassis, continuing the lineage of the 1967 icon. The chassis is modified to house batteries, control modules and four electric motors, providing more torque and four wheel drive. The body panels are now carbon fibre, the suspension - independent and adjustable, the interior - bespoke to the clients styling preference.
Adding an array of tech based features, controls and drivers aids distill the driving experience into its purest form. Updating the design, upgraded the performance and luxury of the iconic Mustang, bringing its classic styling and power into the electrical future of transportation.

Pictured above:
Experimental Prototype 01 (XP01 Mustang Sally) modelled on the mustang from “Gone In 60 Seconds” faces off with a prototype car from Roborace - a AI driverless tech EV racing league, built to rapidly increase the capabilities of driverless cars using motor racing as a driving force. Roborace is a sister company of Charge and as such, they share a lot of cutting edge tech - most notably the batteries, motors and sensors.
Pictured below:
XP01 leaving the unit it was built in for the final time, heading to the new production facility where its successors would be built. Packing and moving all of the equipment, parts, and tools took days. The original unit could fit into the new facility ten times, adding dedicated office and customer spaces, dyno room, parts storage, electronic and mechanical workshops.
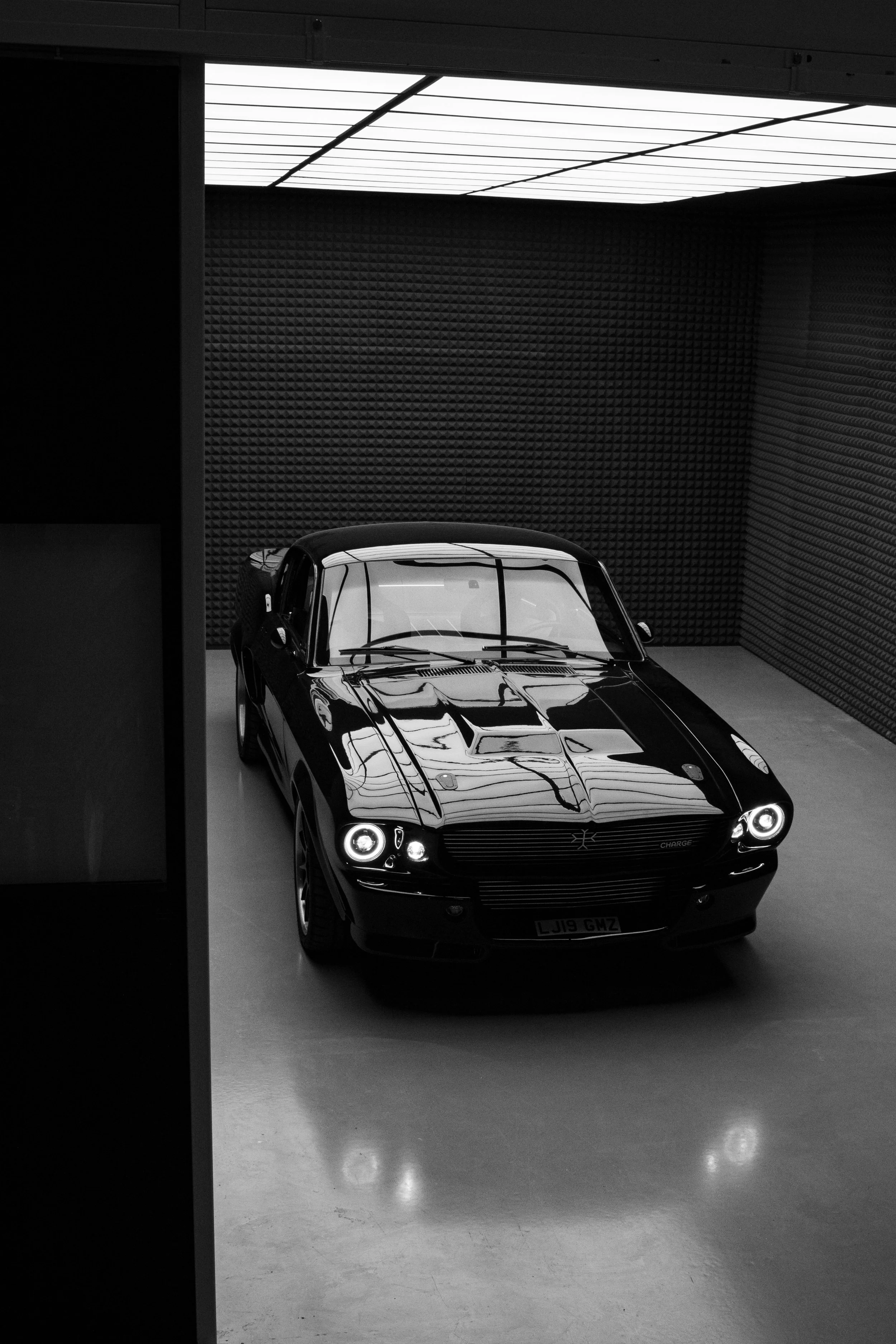
XP01 was used as a proof of concept, to procure investment, to test and redesign the entire car.

An electrical buck was used to build and test all of the systems prior to final design sign off.

The electrical technicians are constantly working on the electrical buck to update it as the design evolves.

The buck was used to prototype the systems for XP01, and will be stripped and restarted for XP02.
Pictured above:
Before the move to the new facility, planning of the workshop and production floor was critical. Ensuring that there was space for 10 cars in various stages of assembly to be built. The production floor had graphics applied to help in the organisation and zoning. Another important aspect was the brand image, as such a graffiti artist was brought in to custom paint the entrance.
Pictured below:
As important as the hardware, is the software that runs the systems. Software engineers are constantly coding, testing and recoding the cars computer to ensure it runs efficiently.

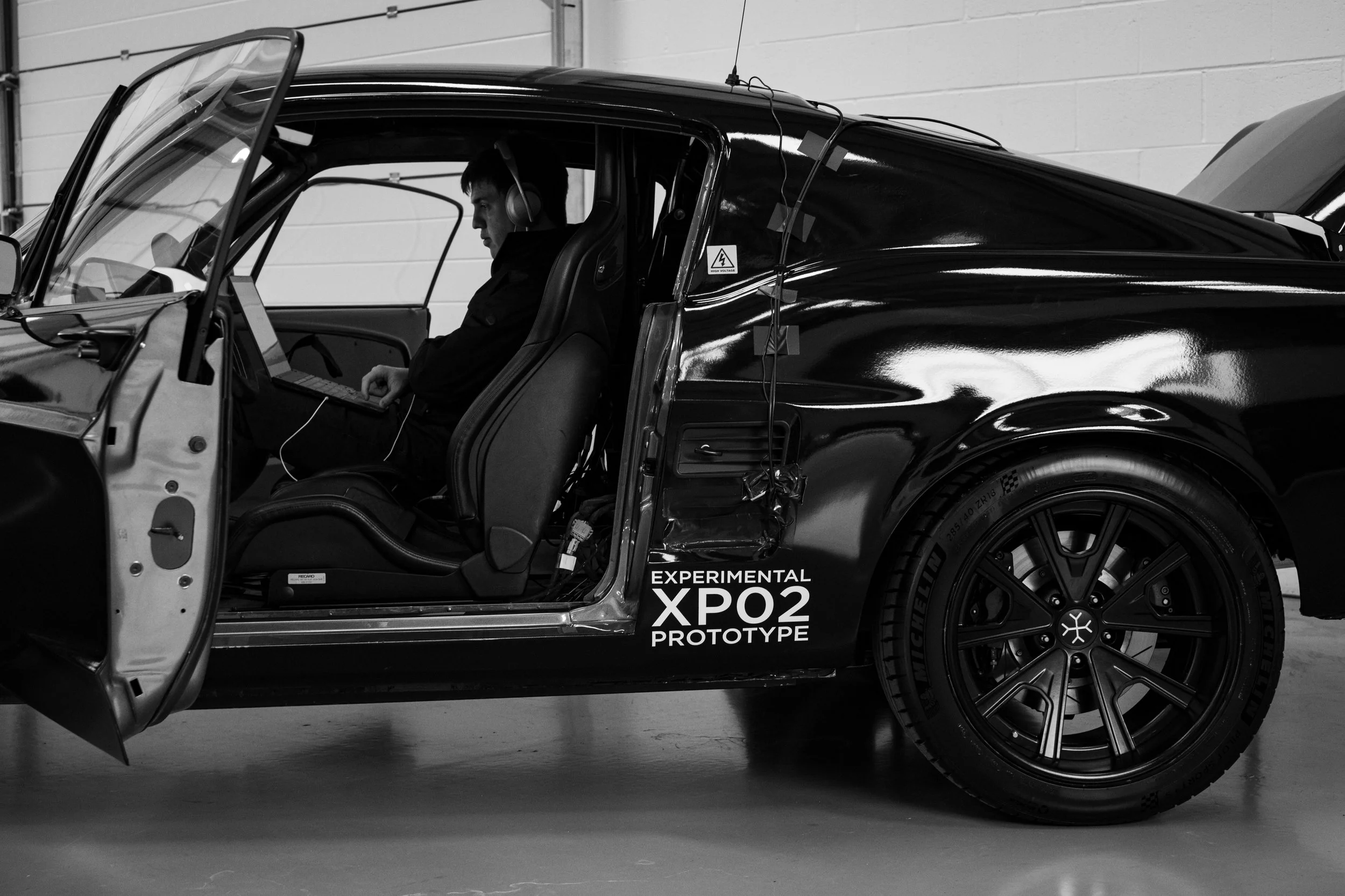
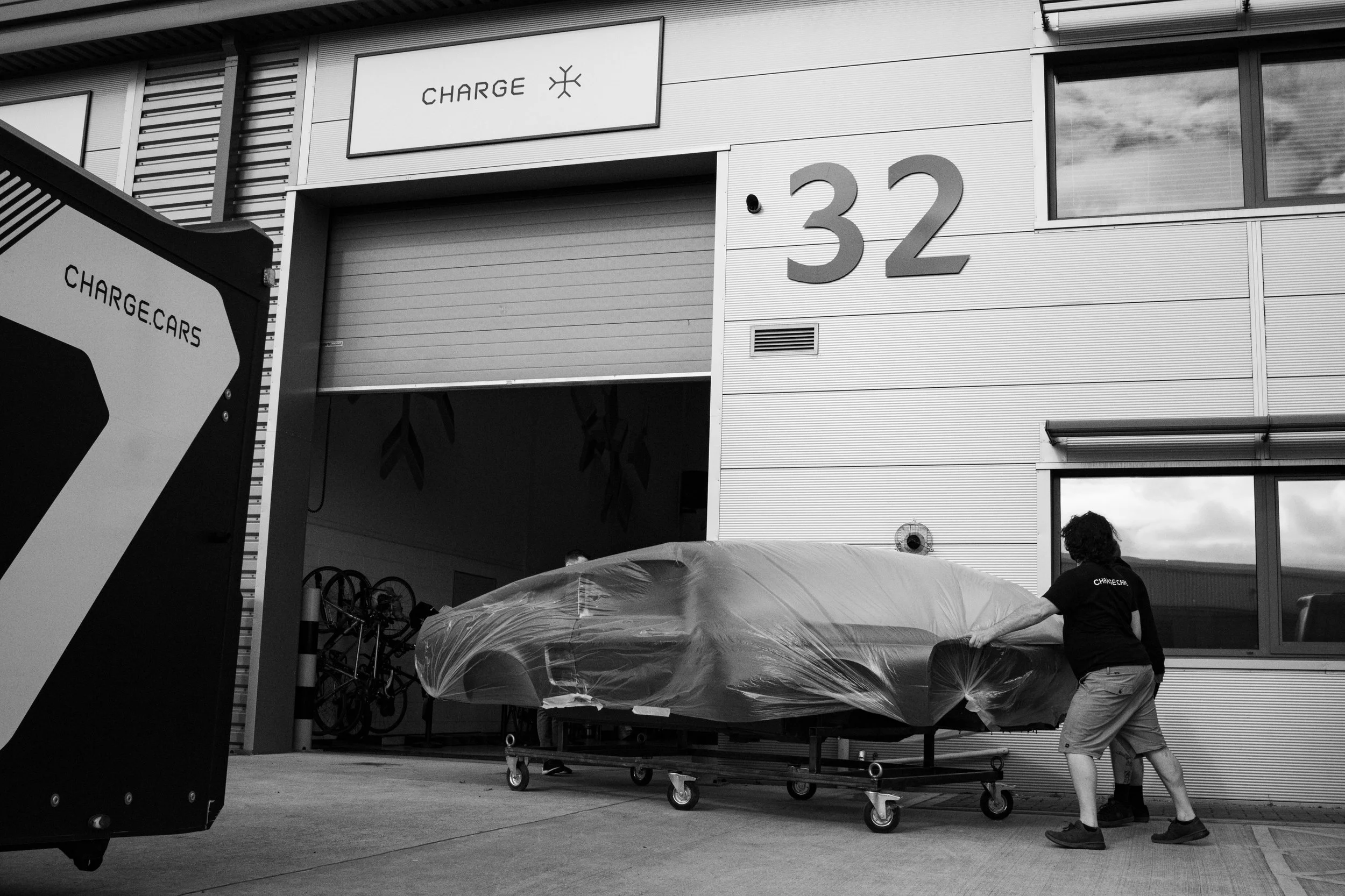
The delivery of a new painted body shell was always an exciting event.

Every team member was eager to assess the colour and quality of the paint.

Due to the clienteles specific paint choices, close inspection for any imperfections was important.

Quality control and providing feedback to the painters ensured flawless results.
Pictured above:
Scanning an Original 1967 Mustang, to compare the straightness of a mid-production, original chassis to the newer Charge chassis. Each Charge chassis was scanned to inform the the jigging and straightening process for the next set of chassis.
Using the original 1967 Mustang tooling came with a few complications, it wasn’t built to todays accuracy and years of use and wear mean that each chassis produced was slightly different. To compensate, straightening jigs were built to produce a more even chassis.
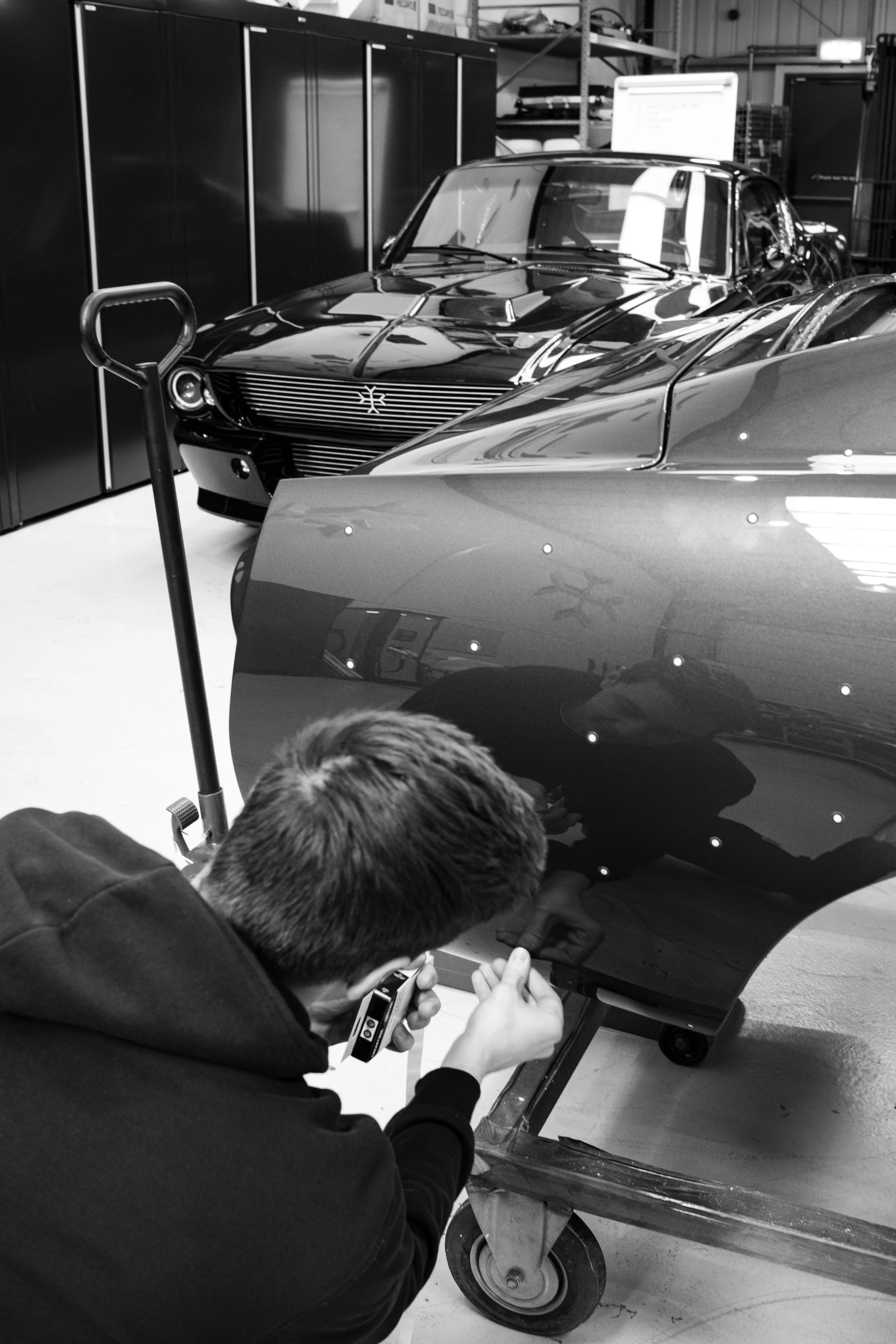
To 3D scan the bodyshells, reflective stickers are randomly placed all over.
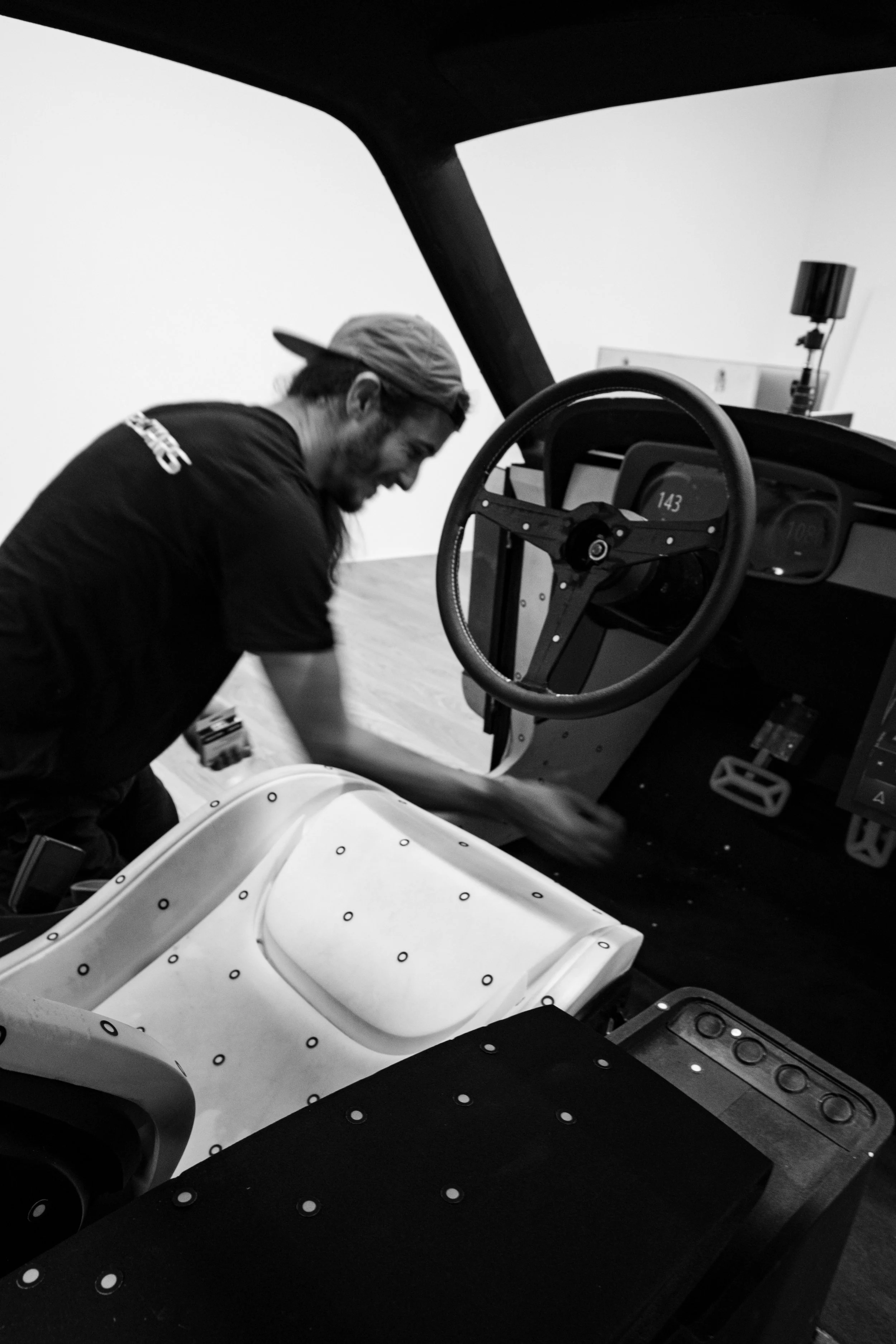
The stickers allow for any surface, regardless of colour or texture to be scanned.
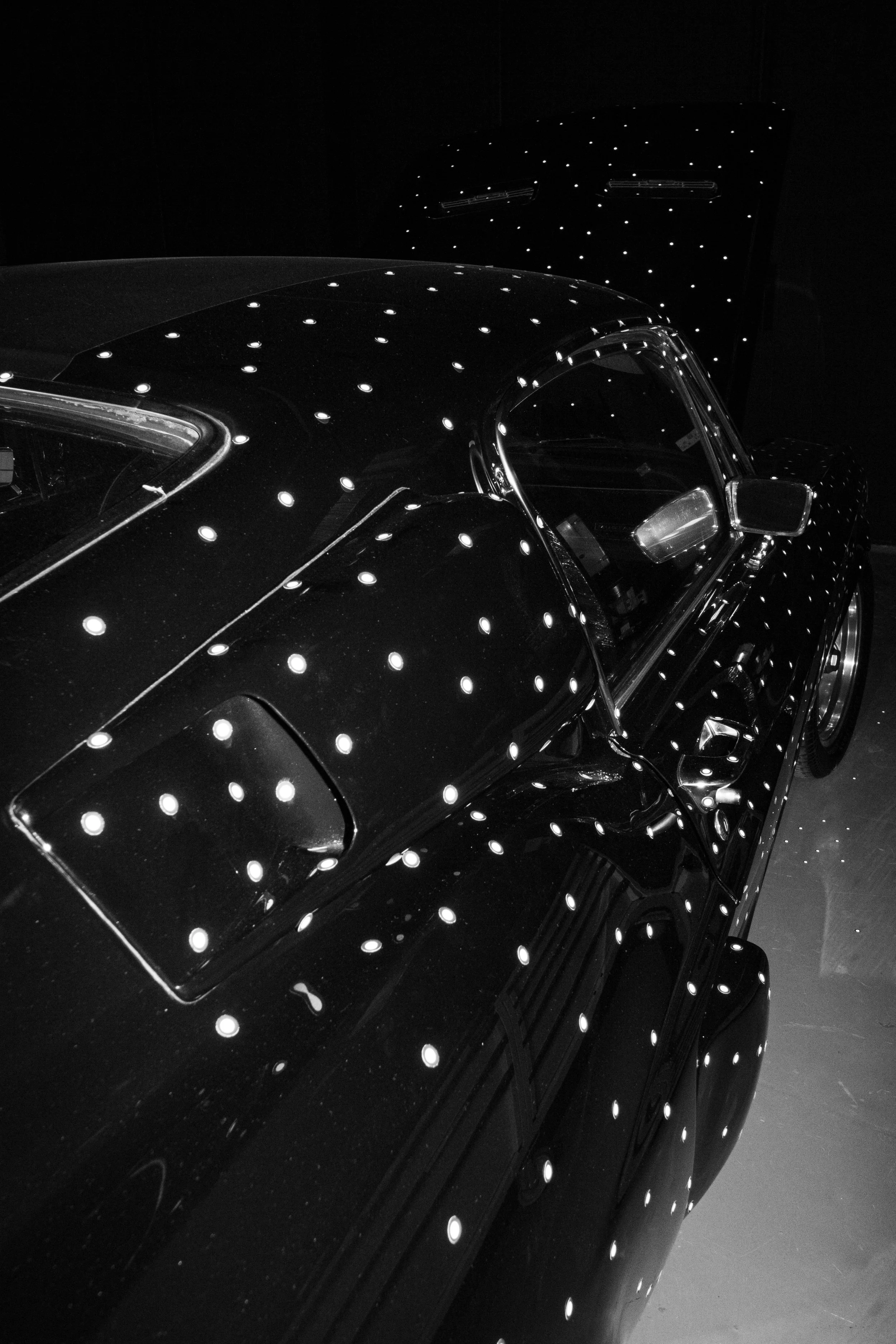
A constellation is created that allows the scanner to map and identify any section of the bodyshell.
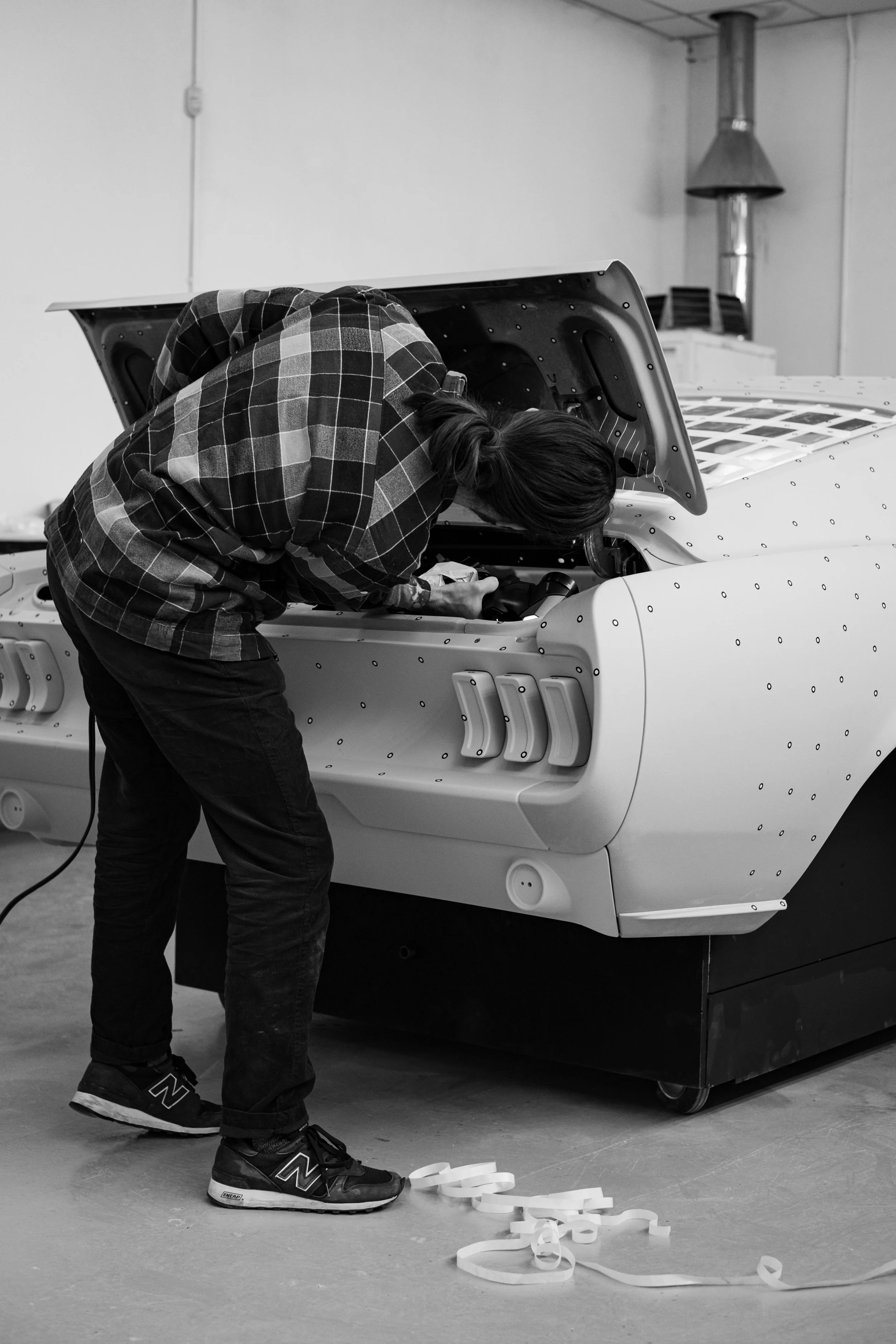
The handheld 3D scanner users lasers to map the surfaces, turning them into a 3D model.
The in-house fabricators build and modify all the custom components until a final design is completed, then the parts are out-sourced to manufacturers to make the final parts. Having the capability to quickly re-engineer and test parts has led to vast improvements in the vehicle handling, ease of assembly and ease of maintenance.
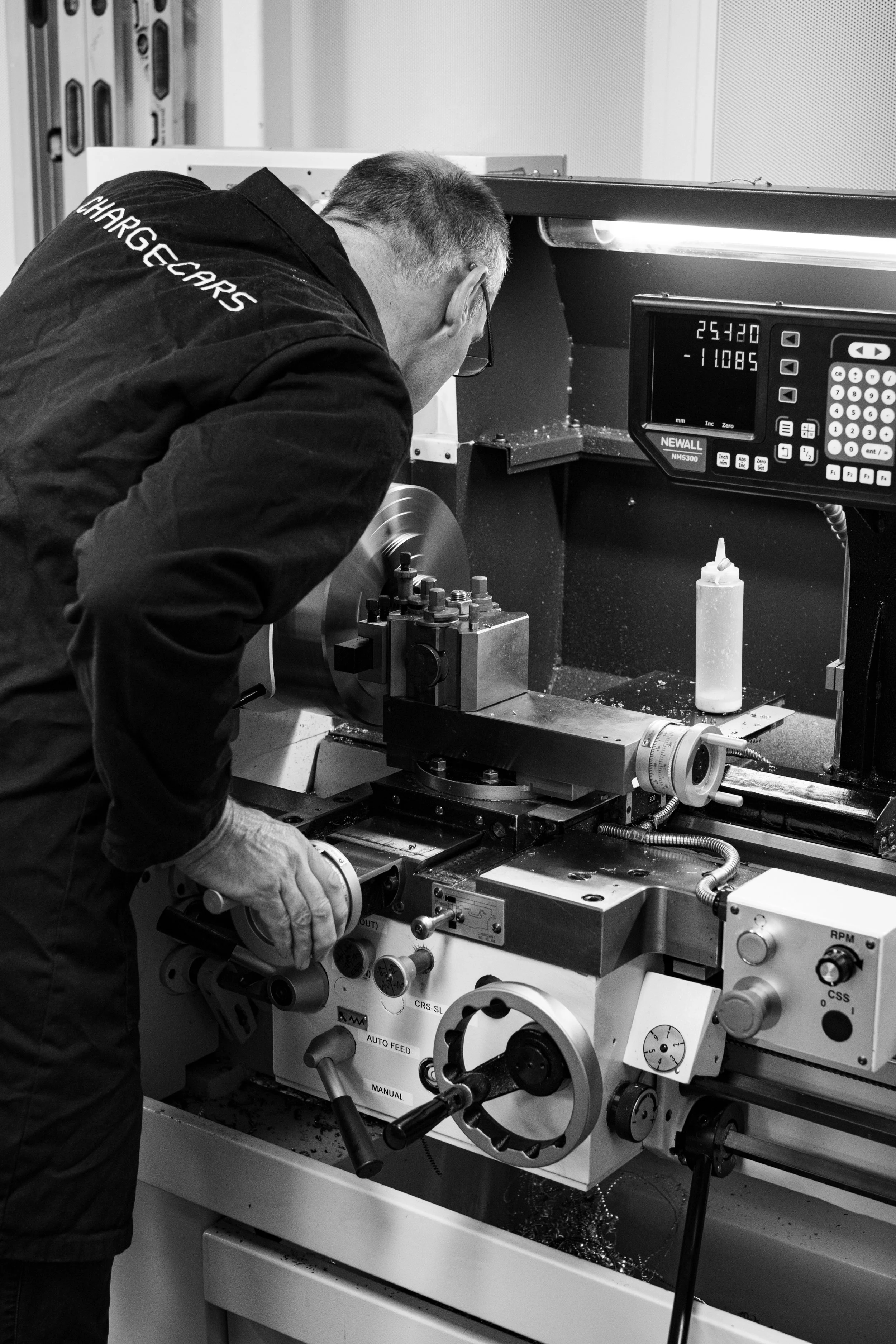

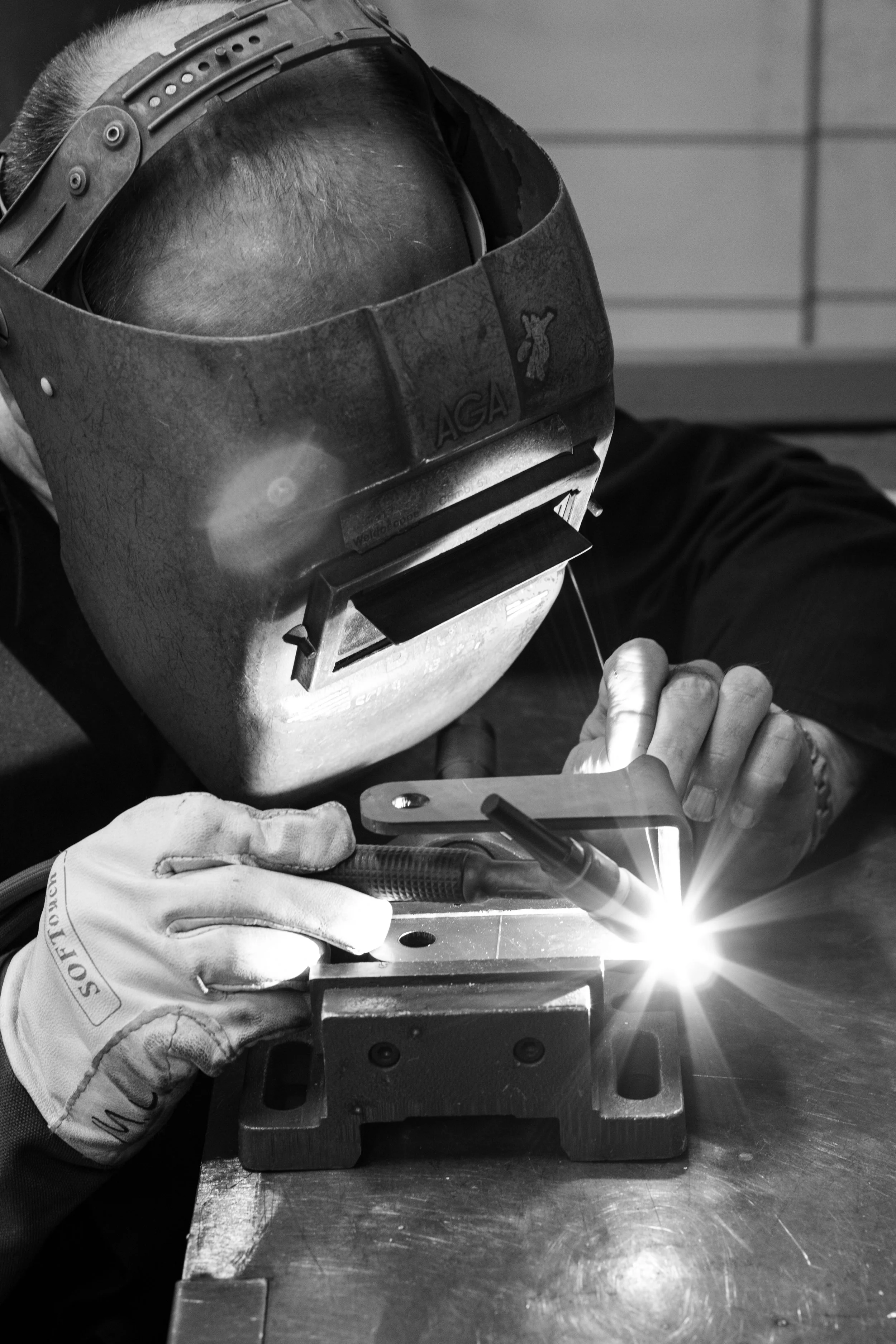




Pictured below:
The rear motor and suspension sub-assembly for the Charge Mustang is a compact and complete system, only requiring a few bolts and the connection of a few wires to be attached and removed. This allows for the rapid removal and maintenance of any parts.

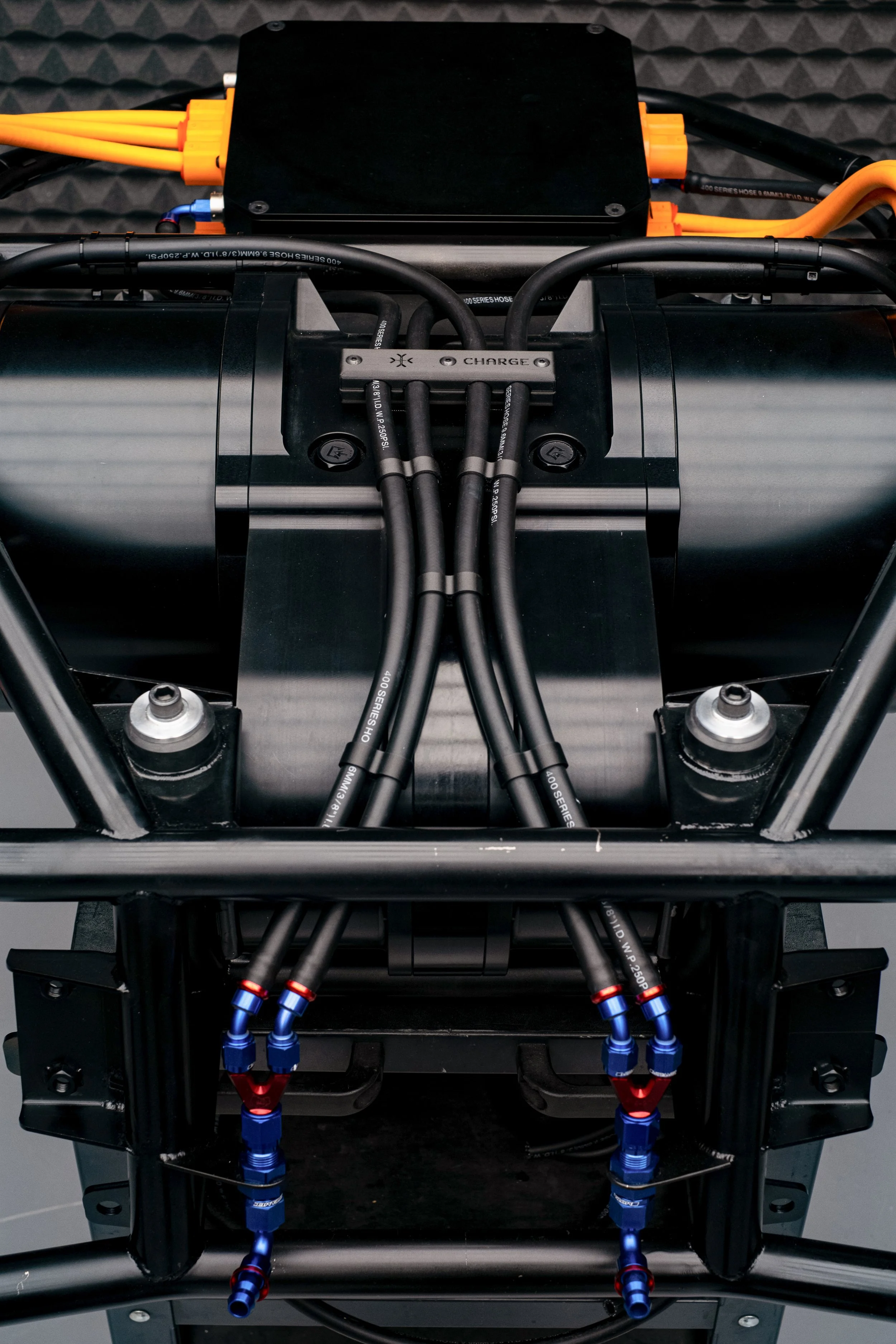
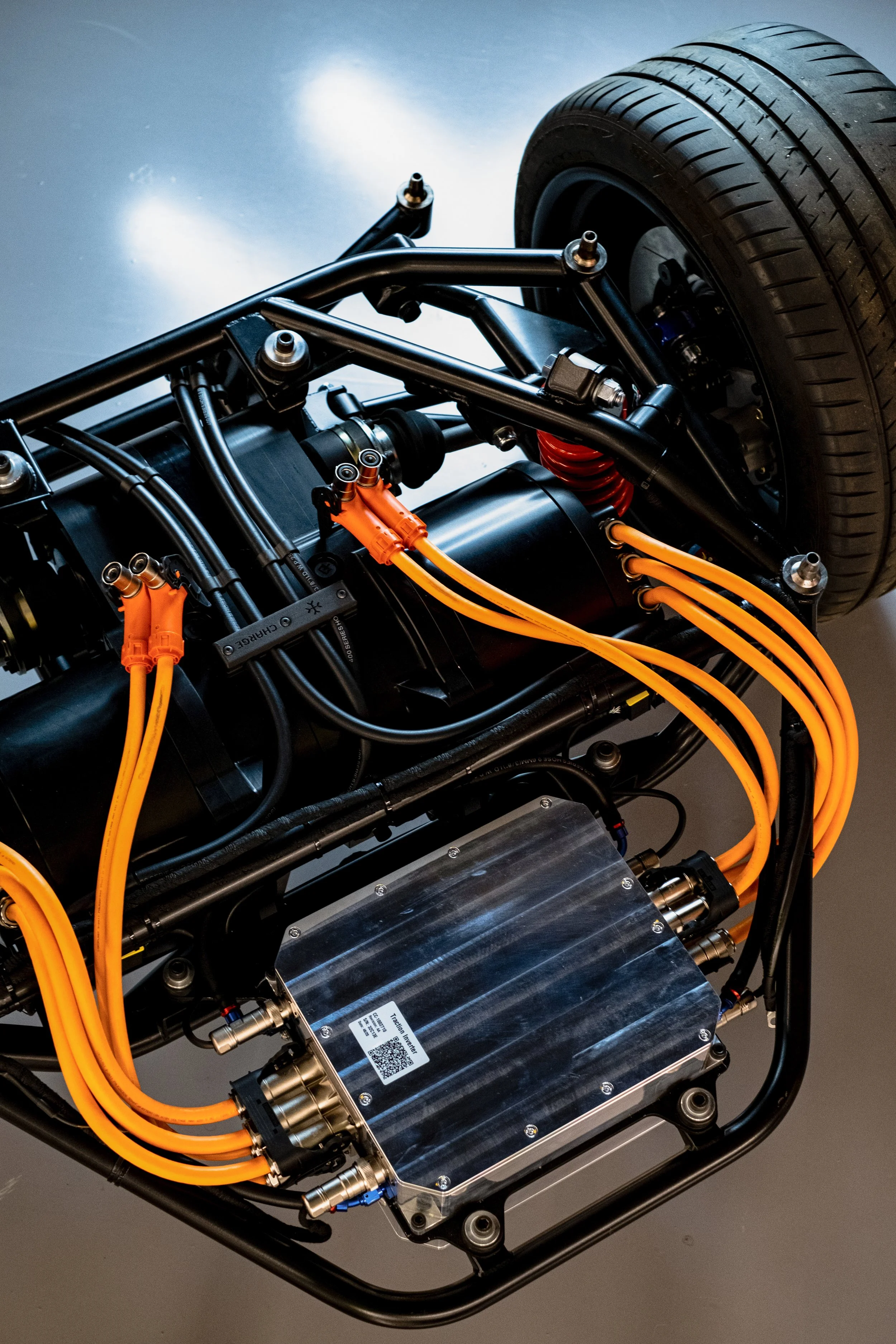


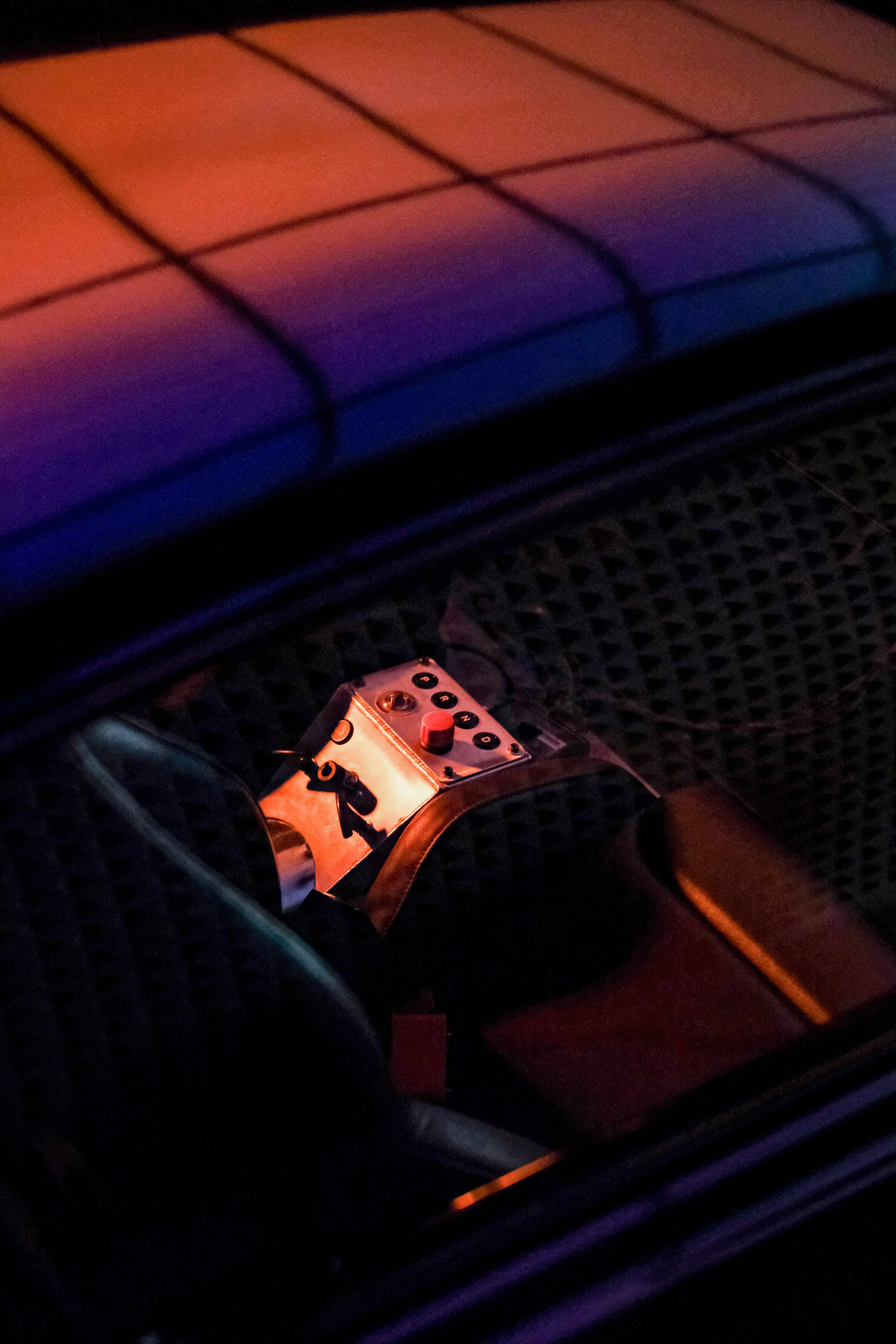
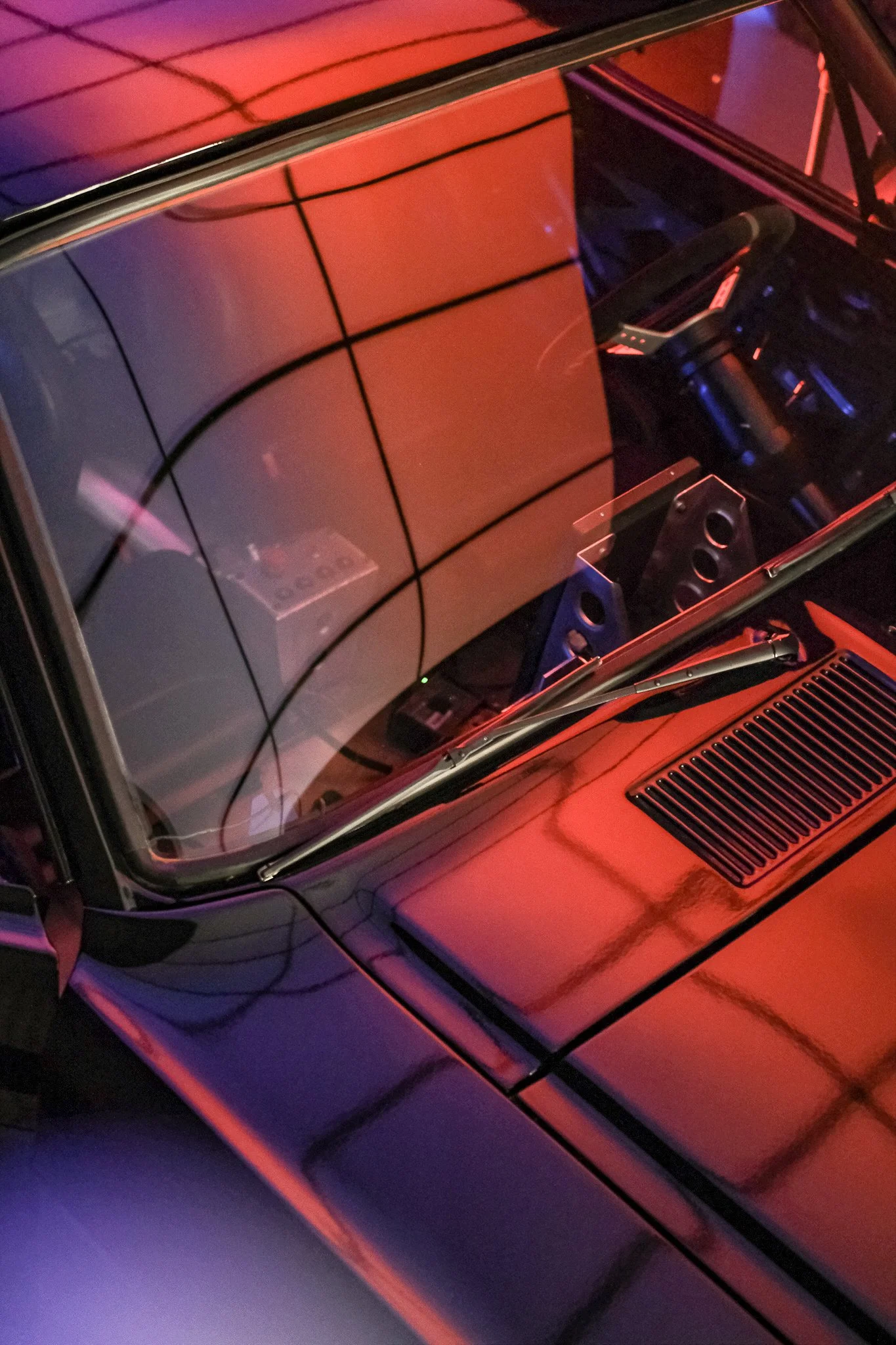
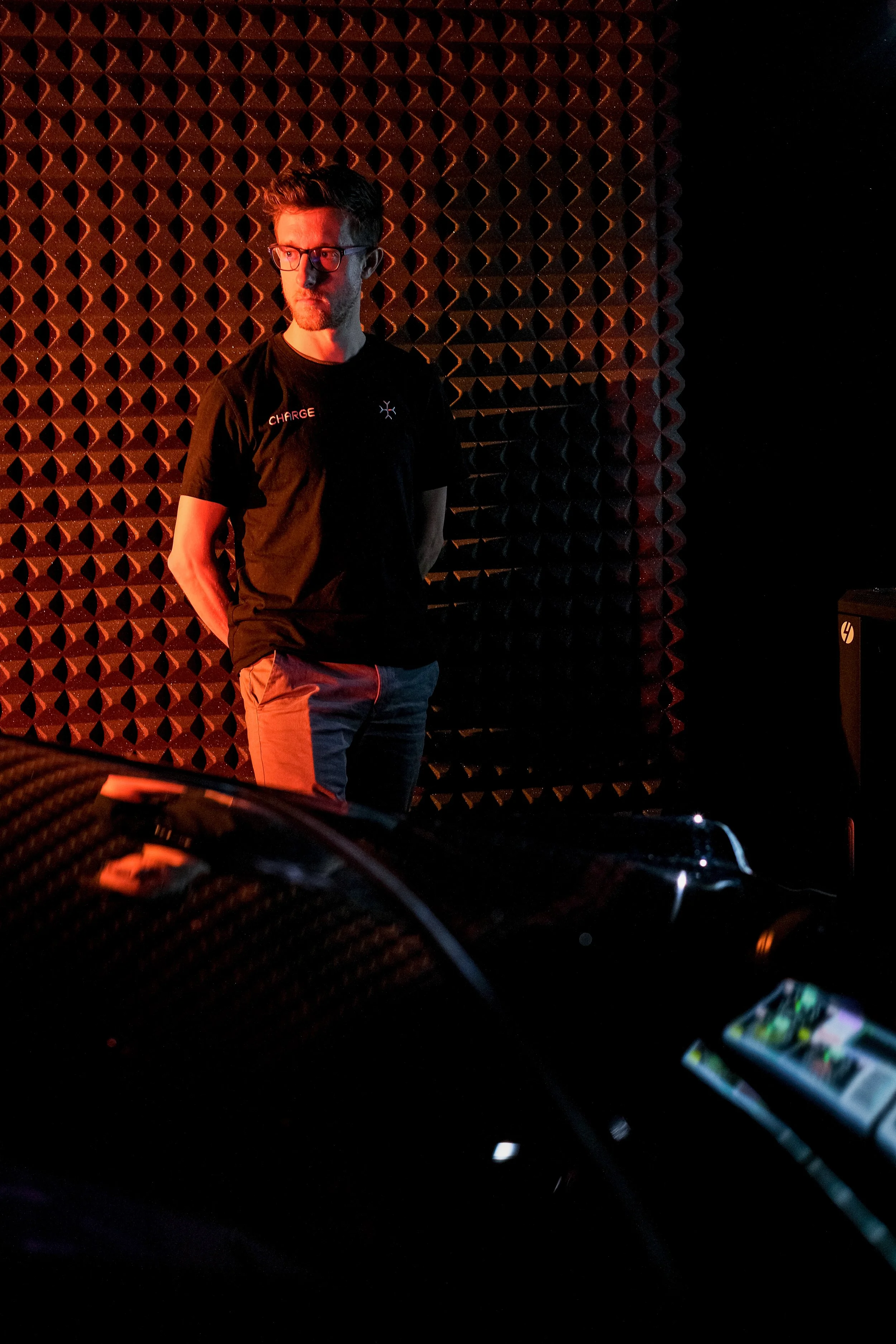







Pictured above:
This prototype brake pedal assembly was manufactured by a computer controlled milling machine. I designed the part to be lightweight yet strong. The final part will have a rubber pedal face for optimum grip.
A team of mechanics are constantly working on the prototype cars, replacing parts as design are updated and ensuring the general maintenance of all prototypes. They are working on multiple prototypes at varying engineering and fabrication stages.

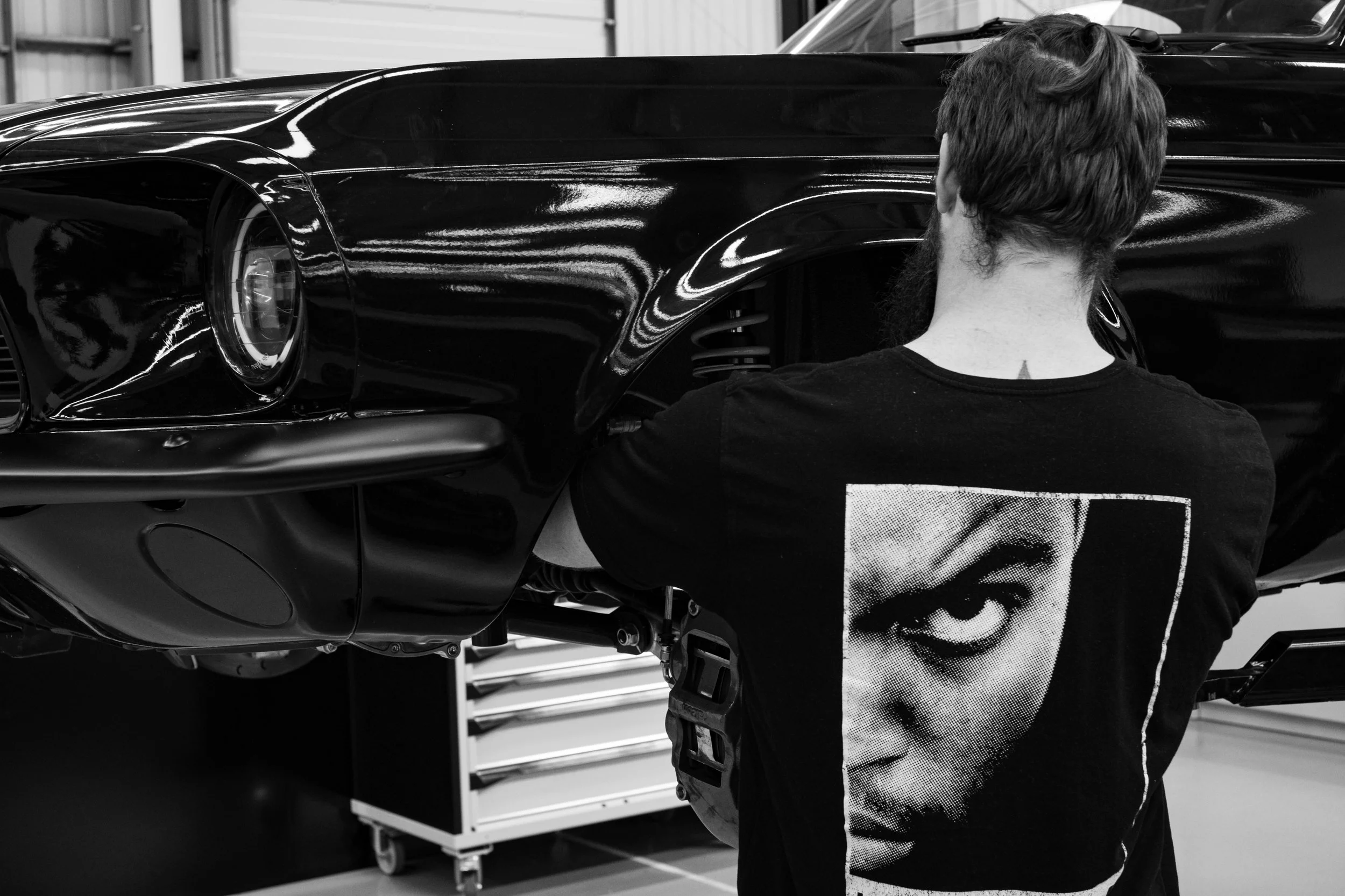

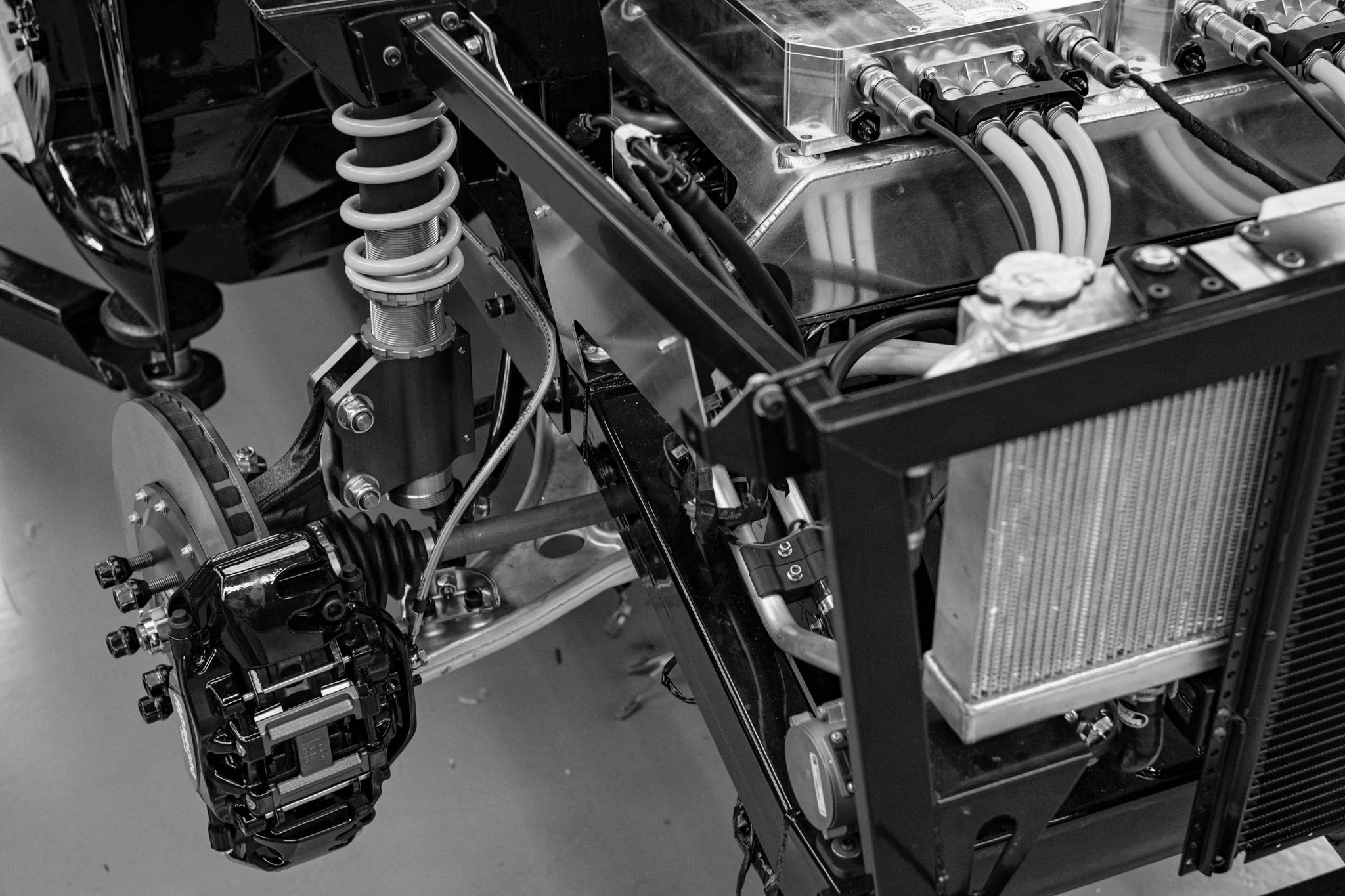



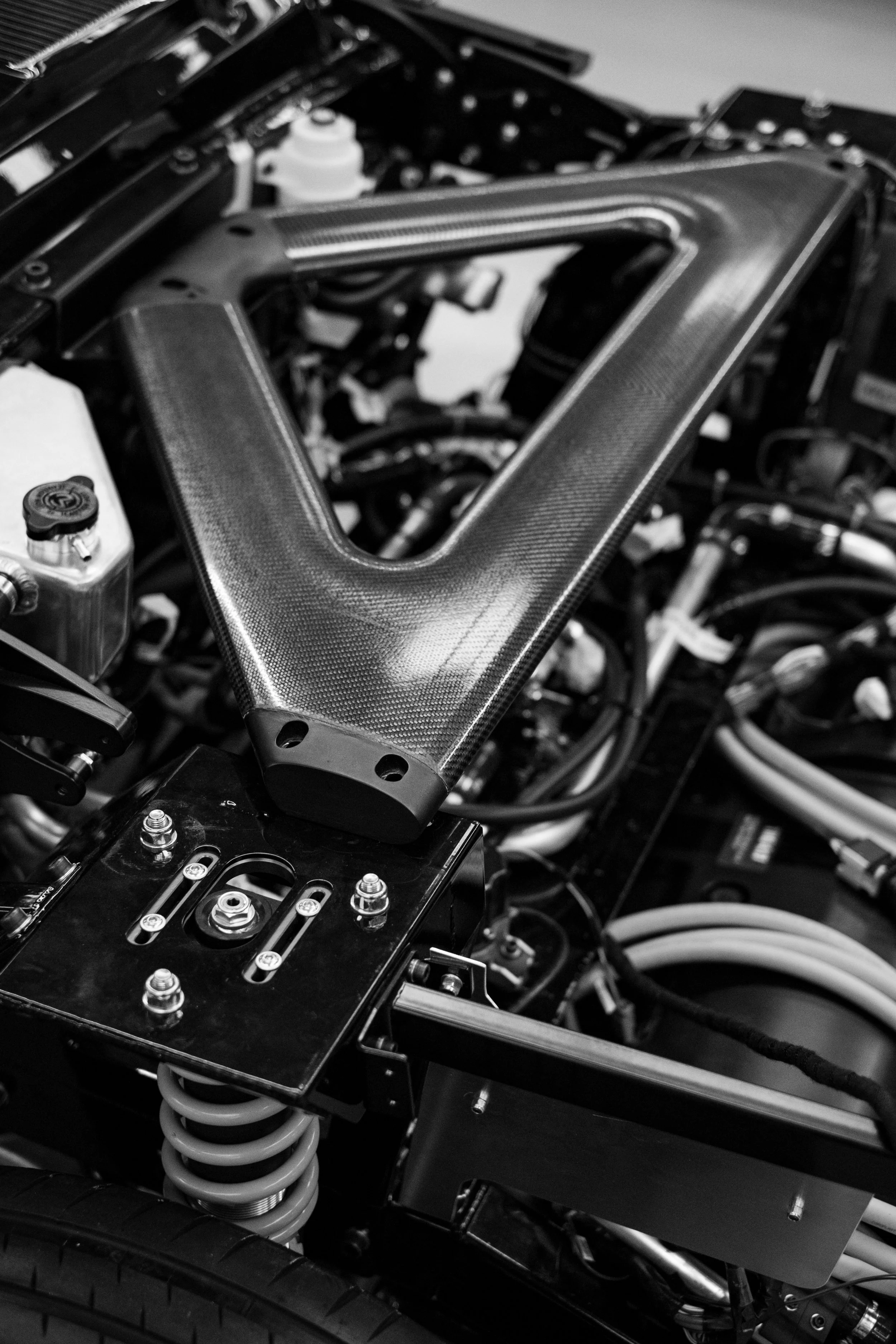
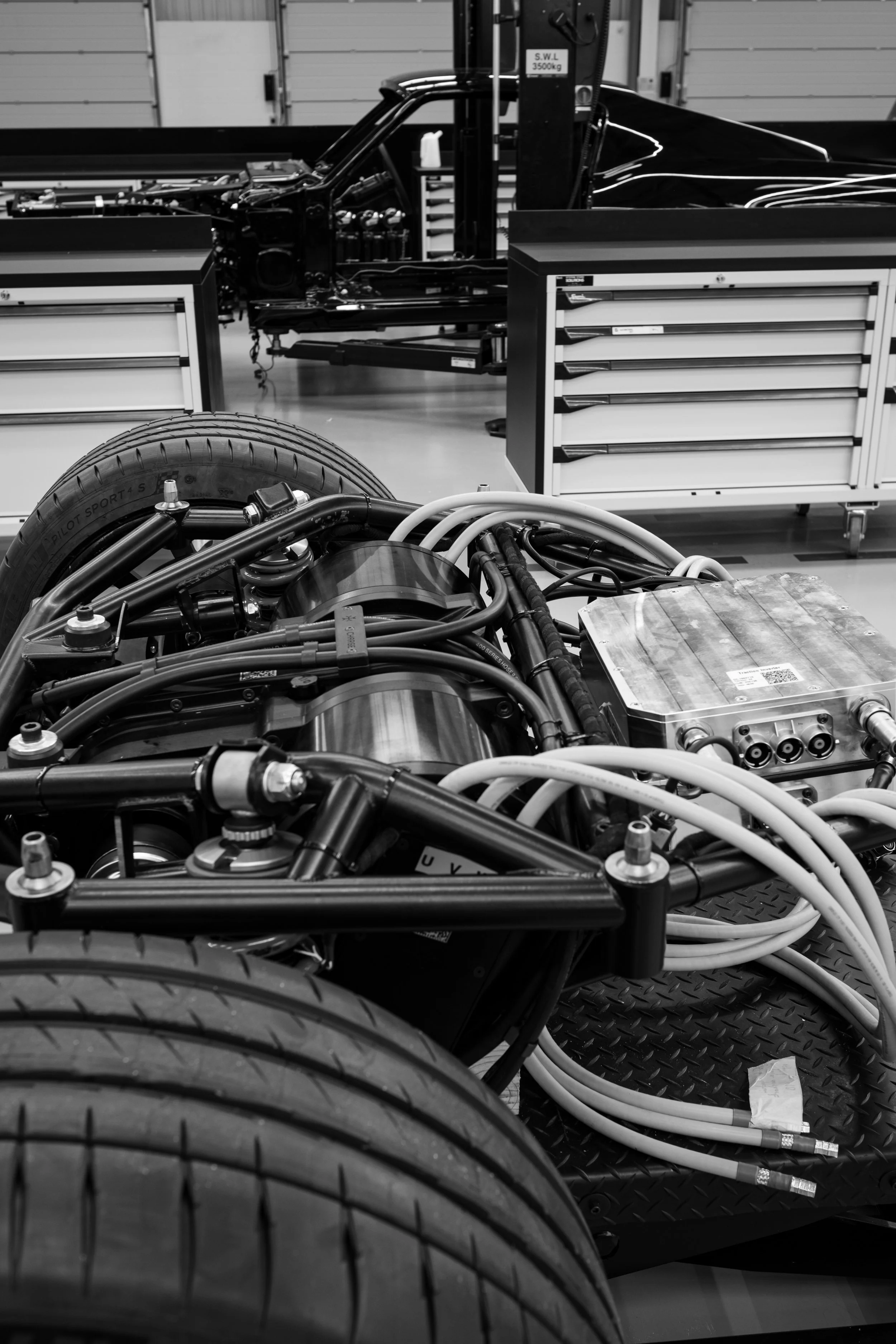


Pictured above and below:
To aid in the production and assembly of each car, there are a set of specific trolleys which are used to manoeuvre and assembly different parts and sub-assemblies onto the chassis. Each car has its own build bay, tool chests, trolleys and mechanics.
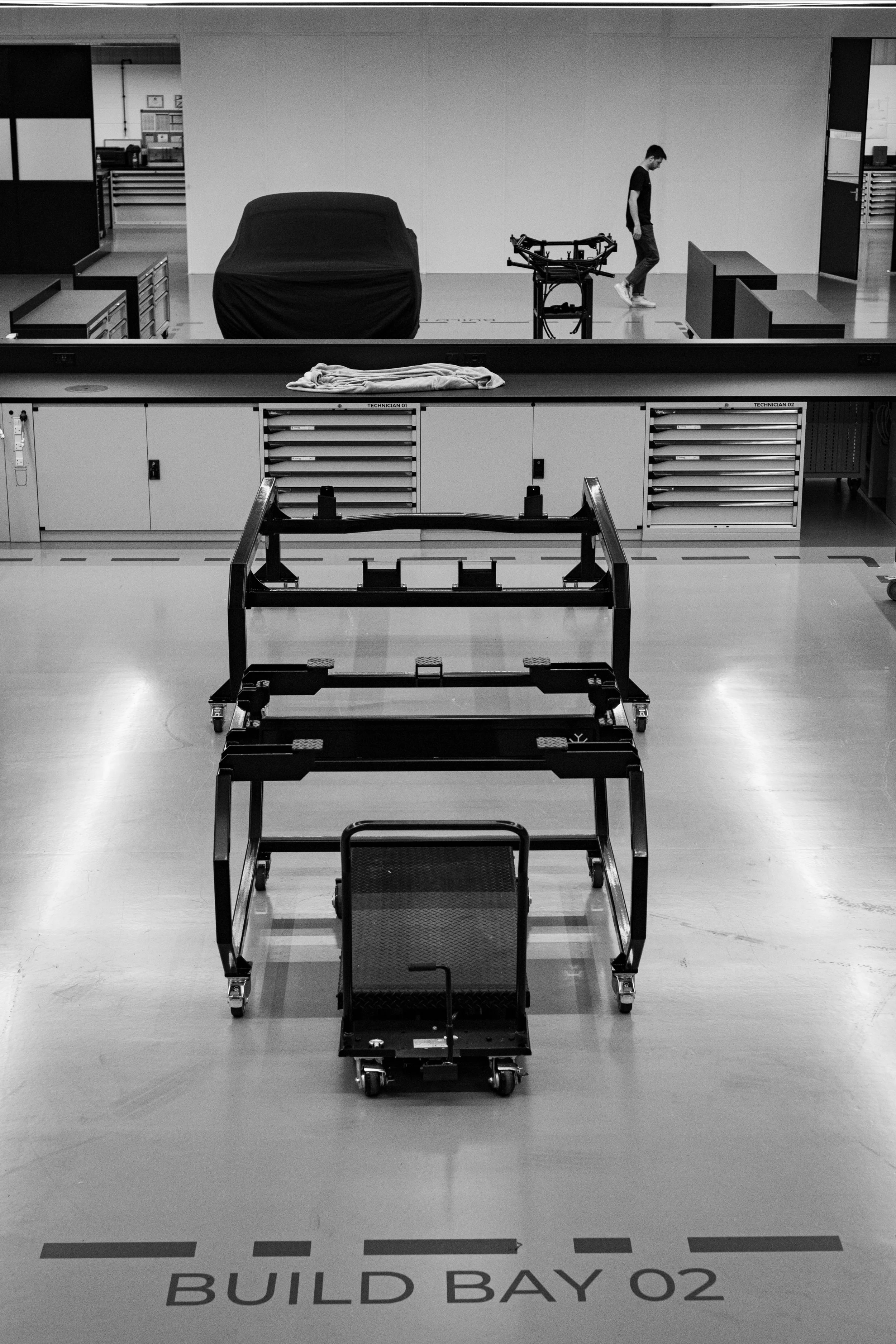

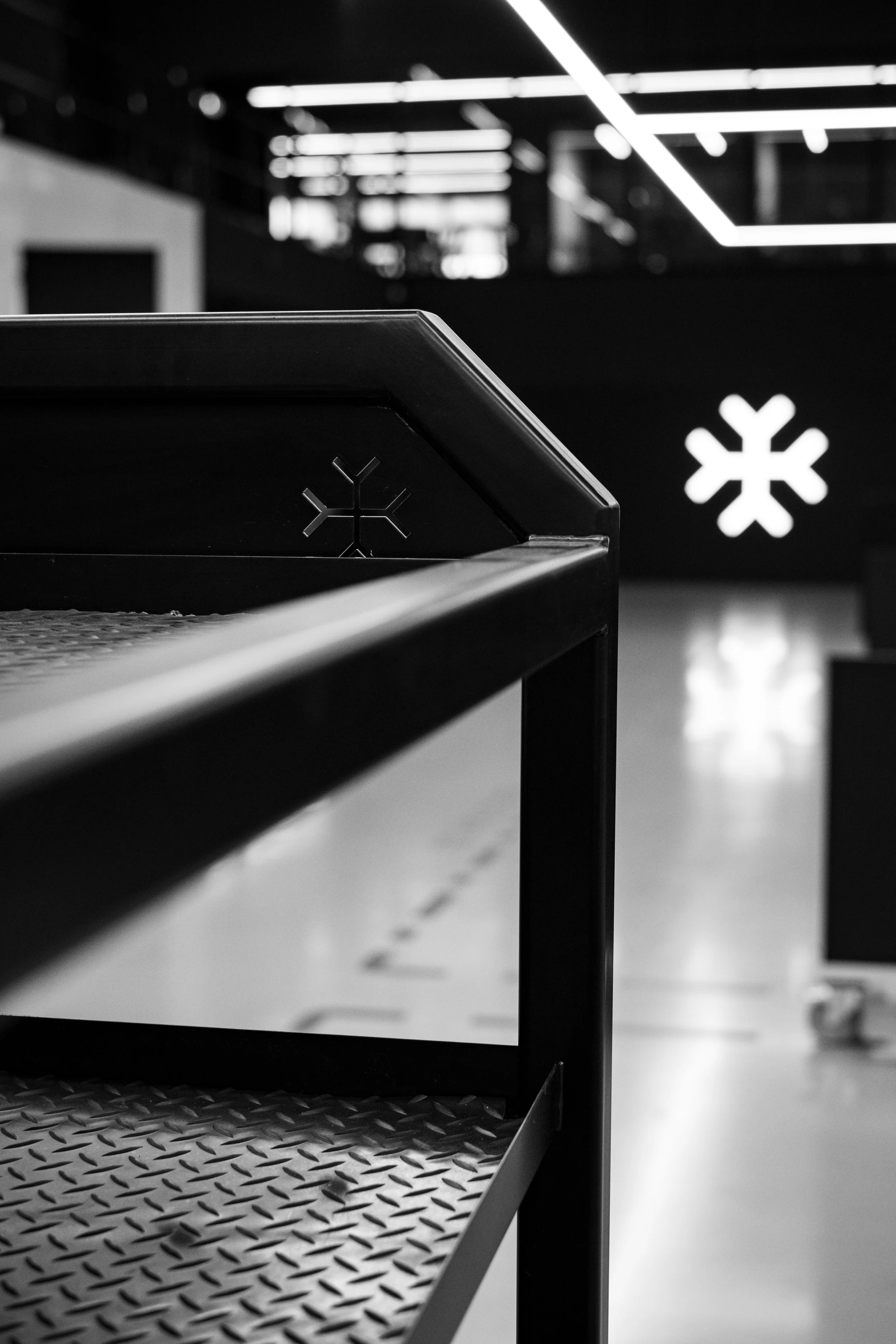
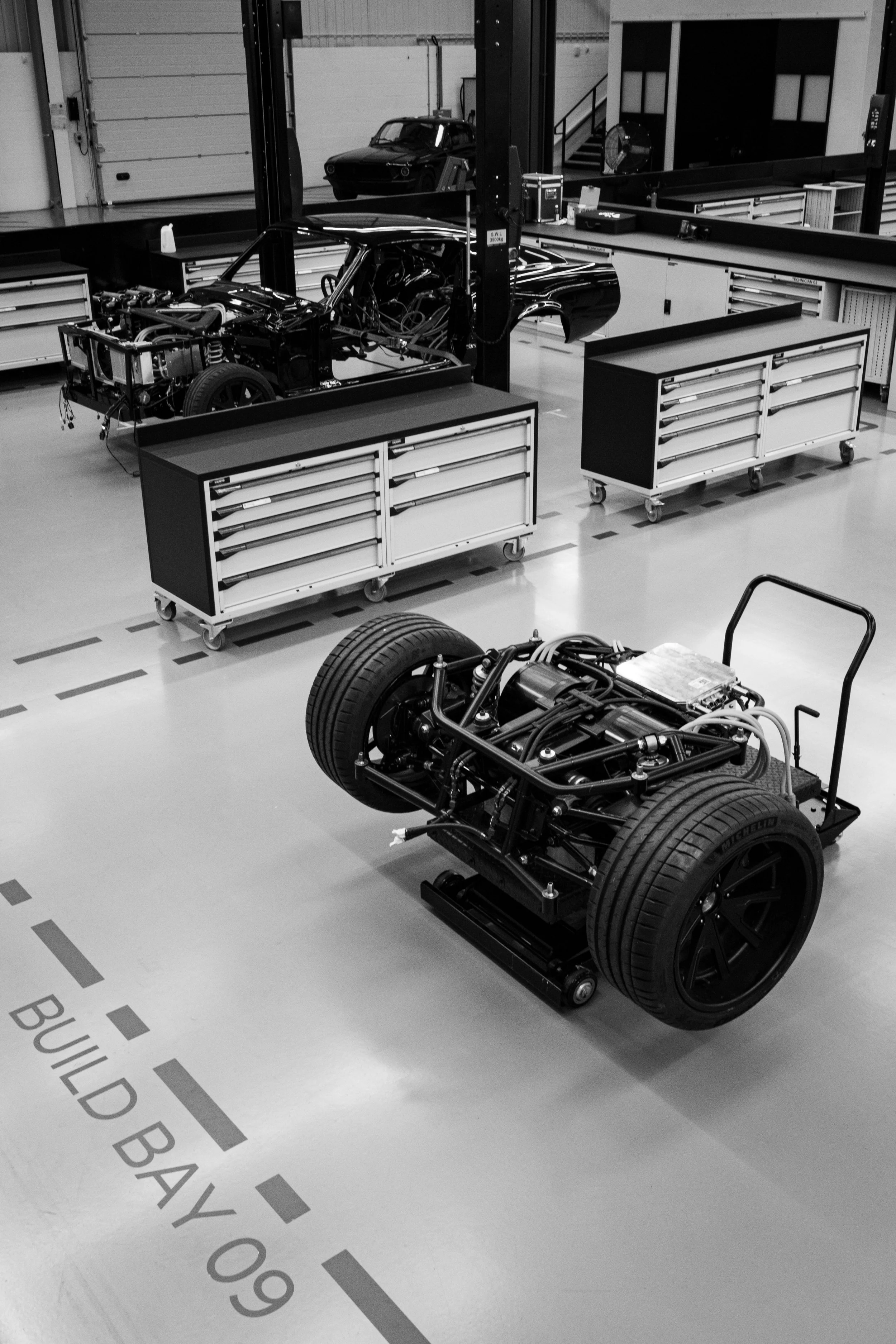
Pictured above and below:
At the new production facility is a dedicated dyno room, this allows the team to run power tests in-house, allowing them to make rapid software tweaks.
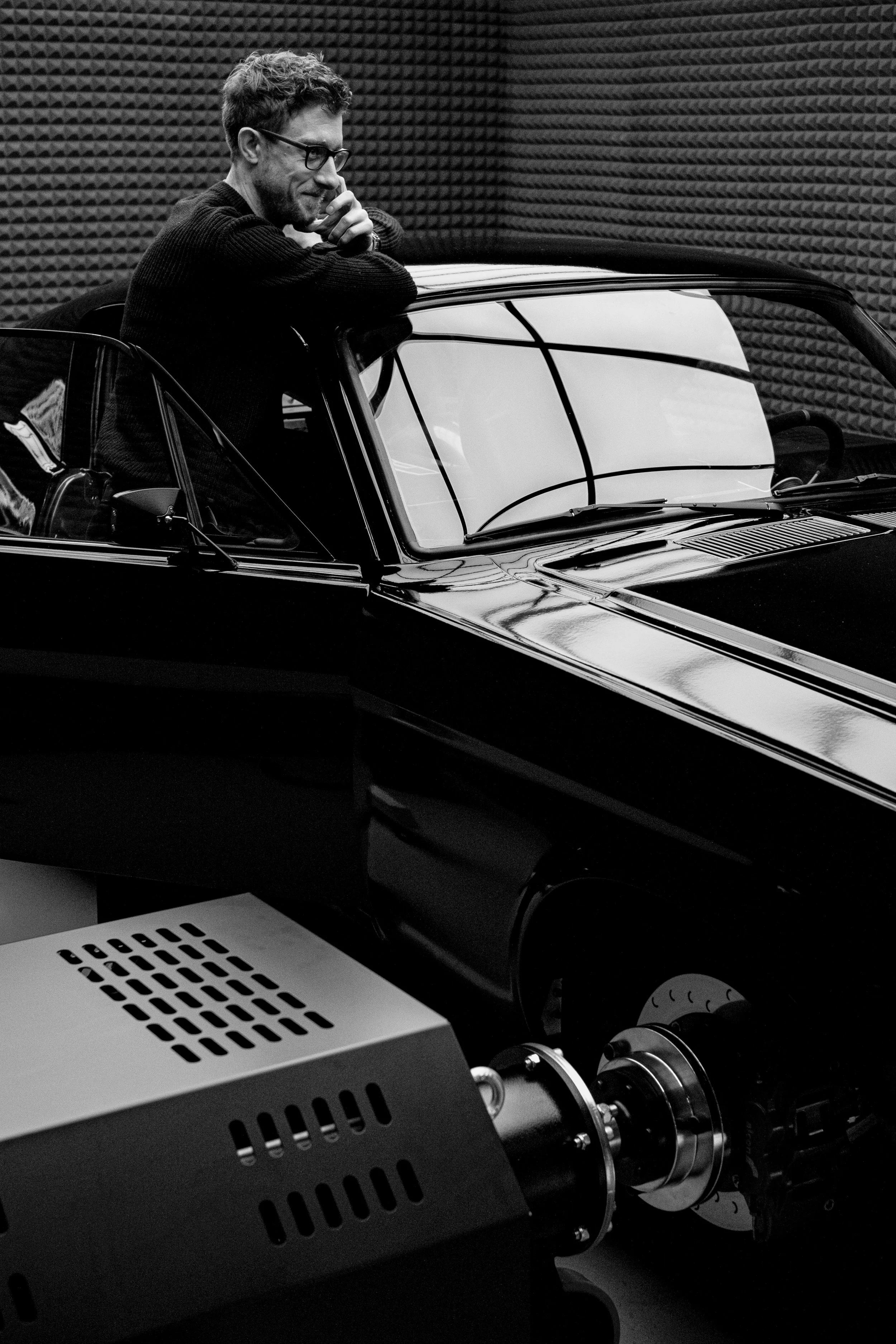



Pictured above and below:
These are Roborace’s Gen 1 EV, autonomous, driverless race cars. They are part of a race league created to challenge and rapidly increase the performance of autonomous driving software. The Charge Mustang and these Roborace cars share the same motor, battery and sensor technology, therefore putting the Mustang at the forefront of EV tech.
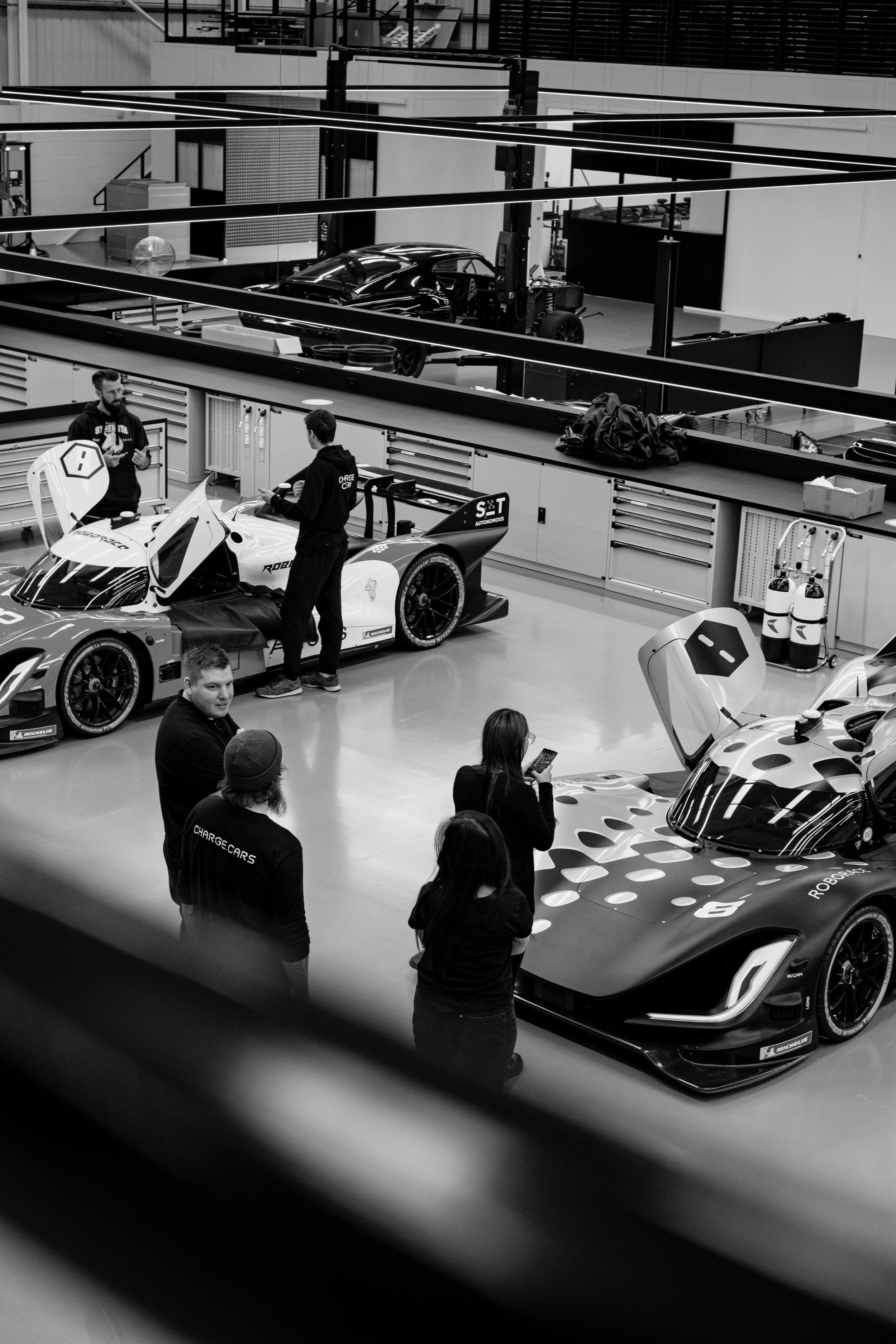
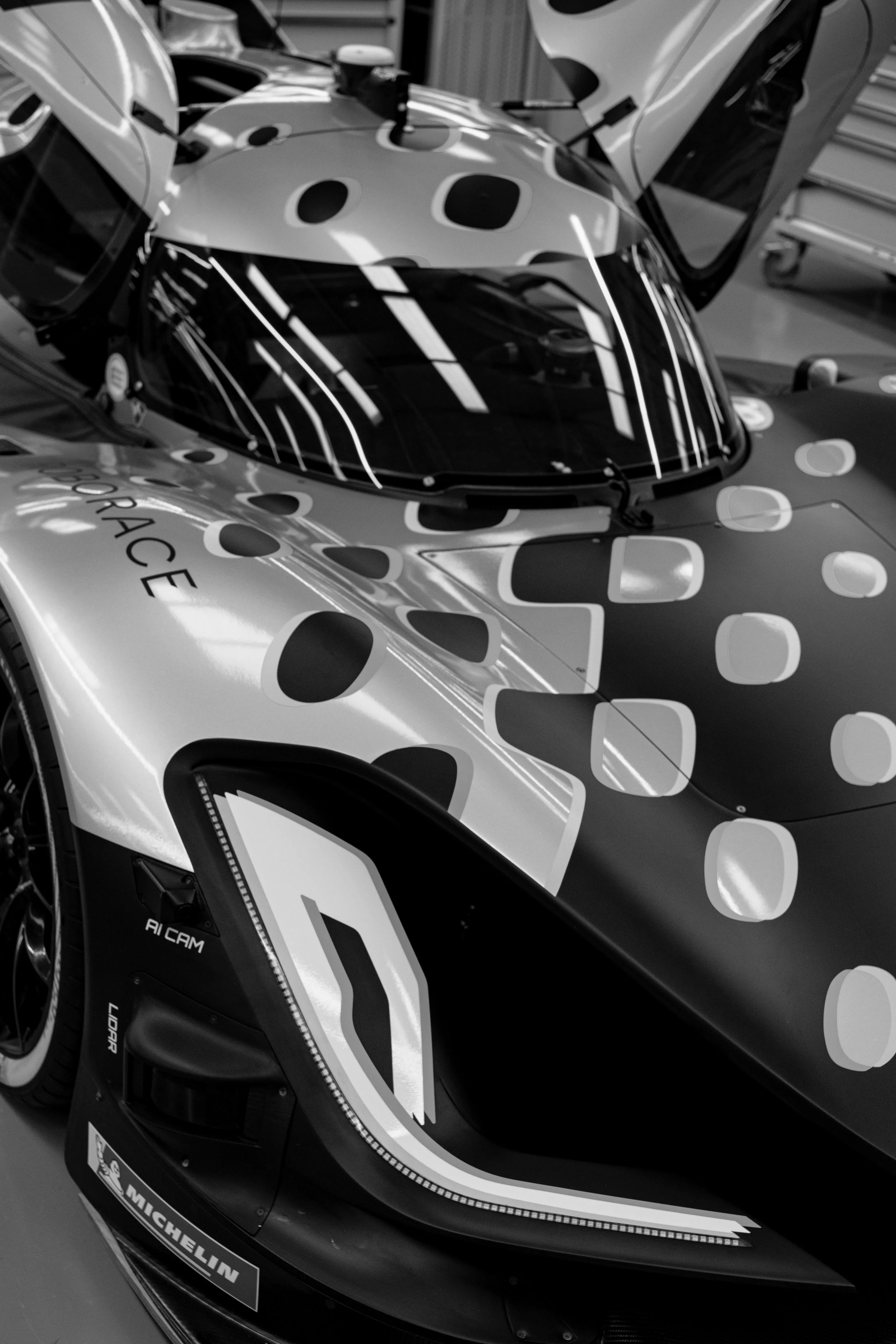
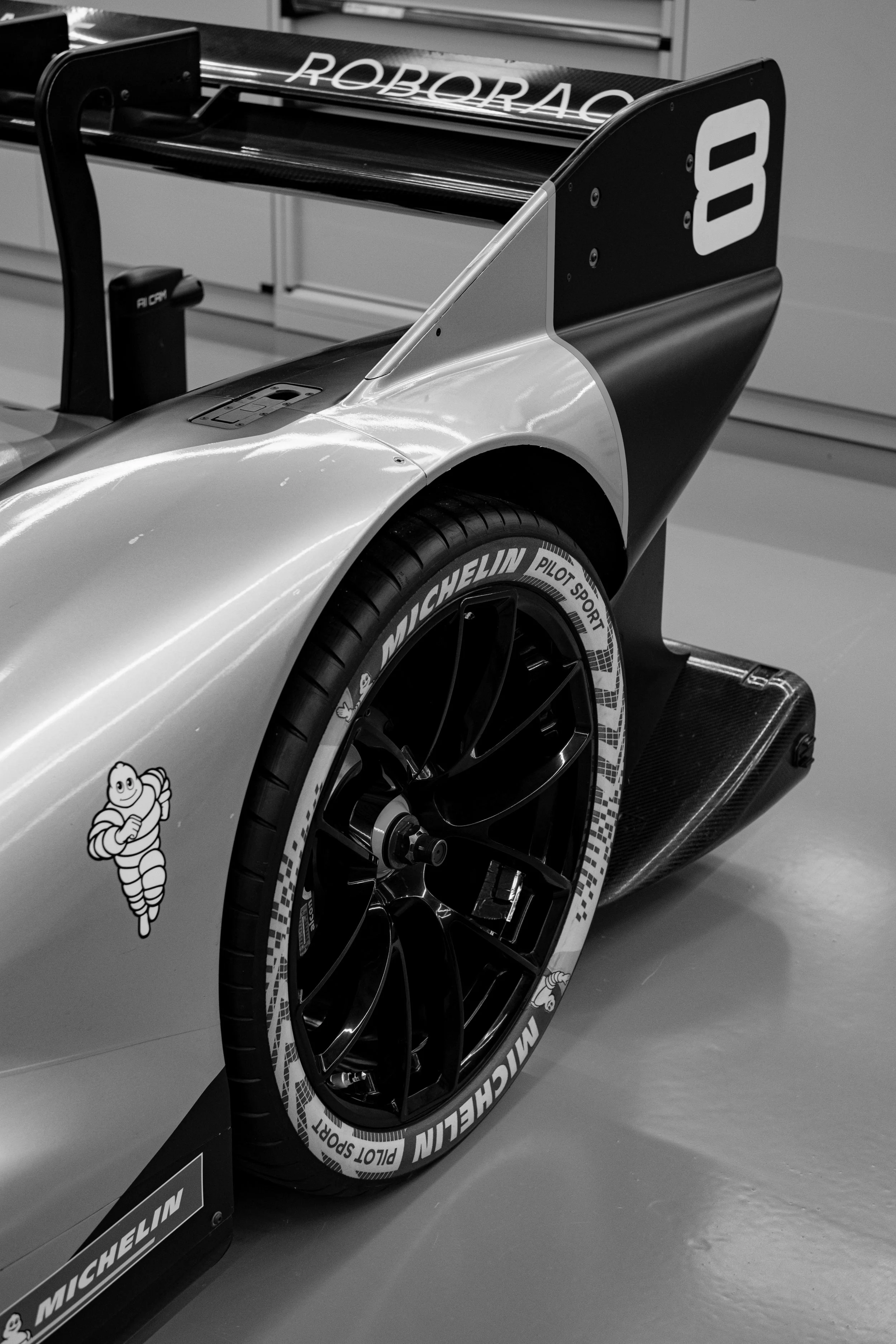

Pictured above and below:
Prepping the Charge Mustang for a track day, to test the suspension, hard and software. The Mustang is charged up, before being loaded onto a trailer and driven to the track. Pre-test checks on the wheel bolt torques, coolant levels etc are carried out before the Mustang is put through a series of rigorous tests. Testing the acceleration, braking, handling and high speed runs provides plenty of data for the team to assess and modify any aspect of the cars performance,


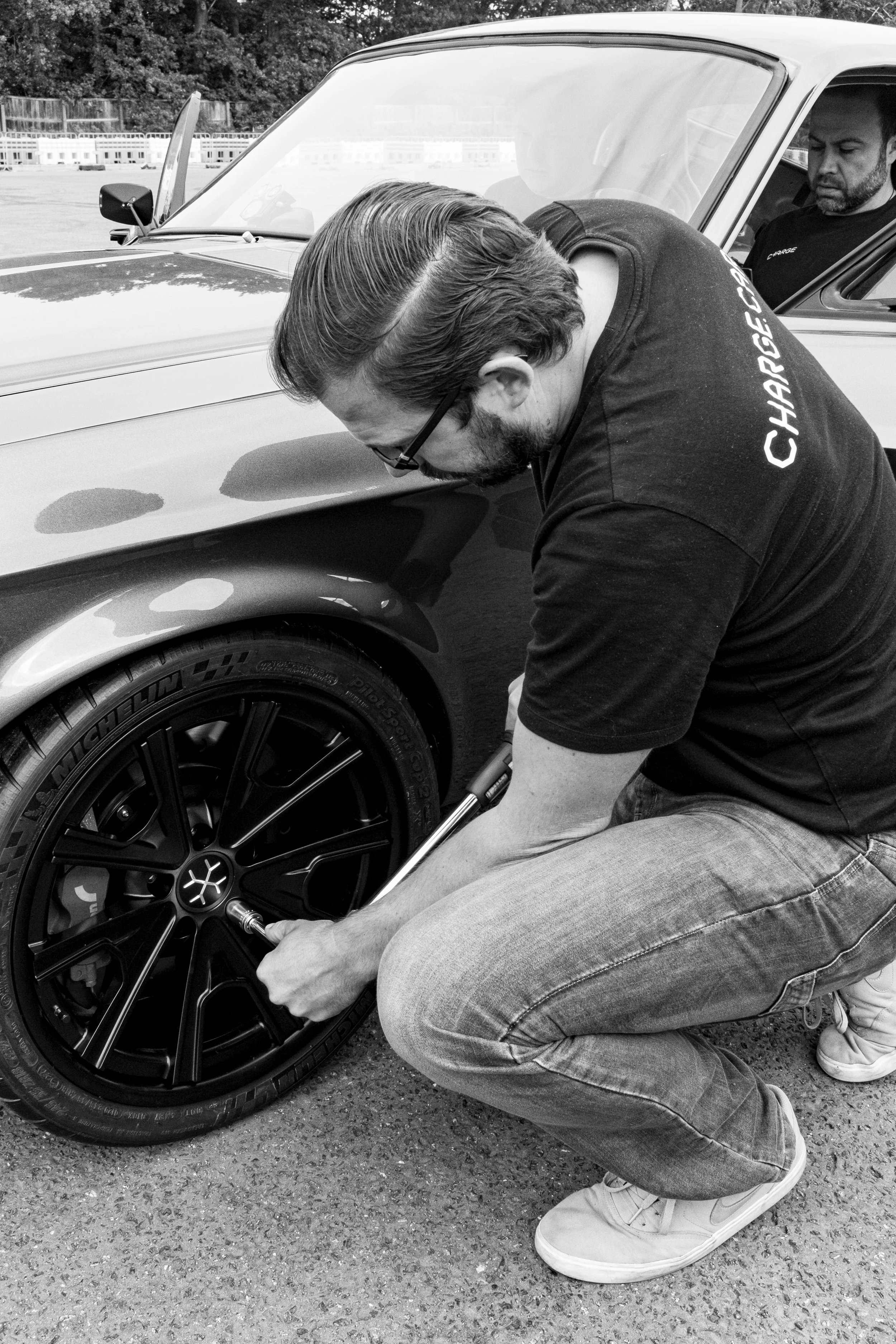




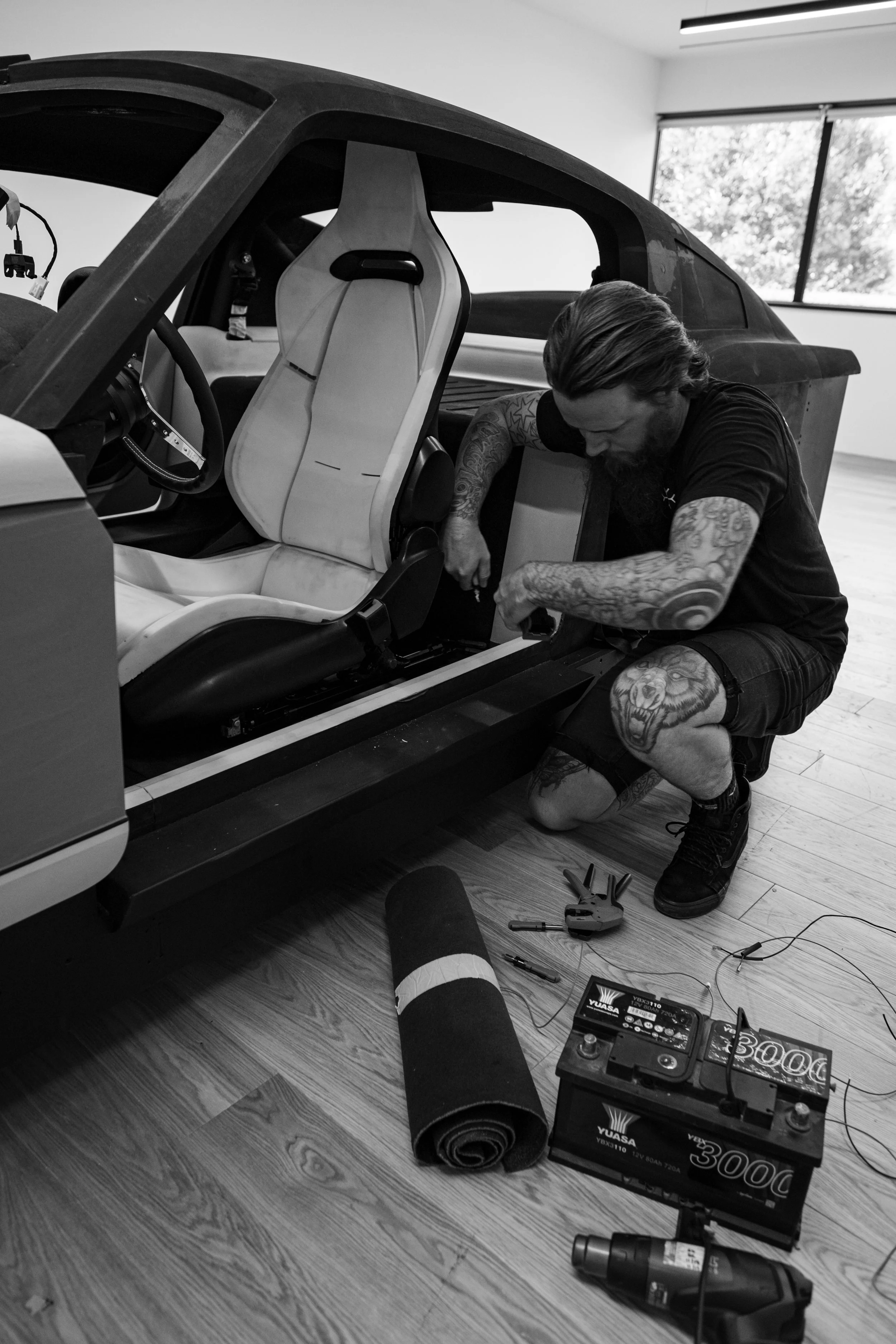
Pictured above:
Quarterly team meetings at charge were always a celebrated event, in the new facility they became a spectacle, with each team presenting the progress they had achieved surrounded by the cars they were designing and building. After the conclusion of the meeting, there were food trucks and entertainment for the team to celebrate.

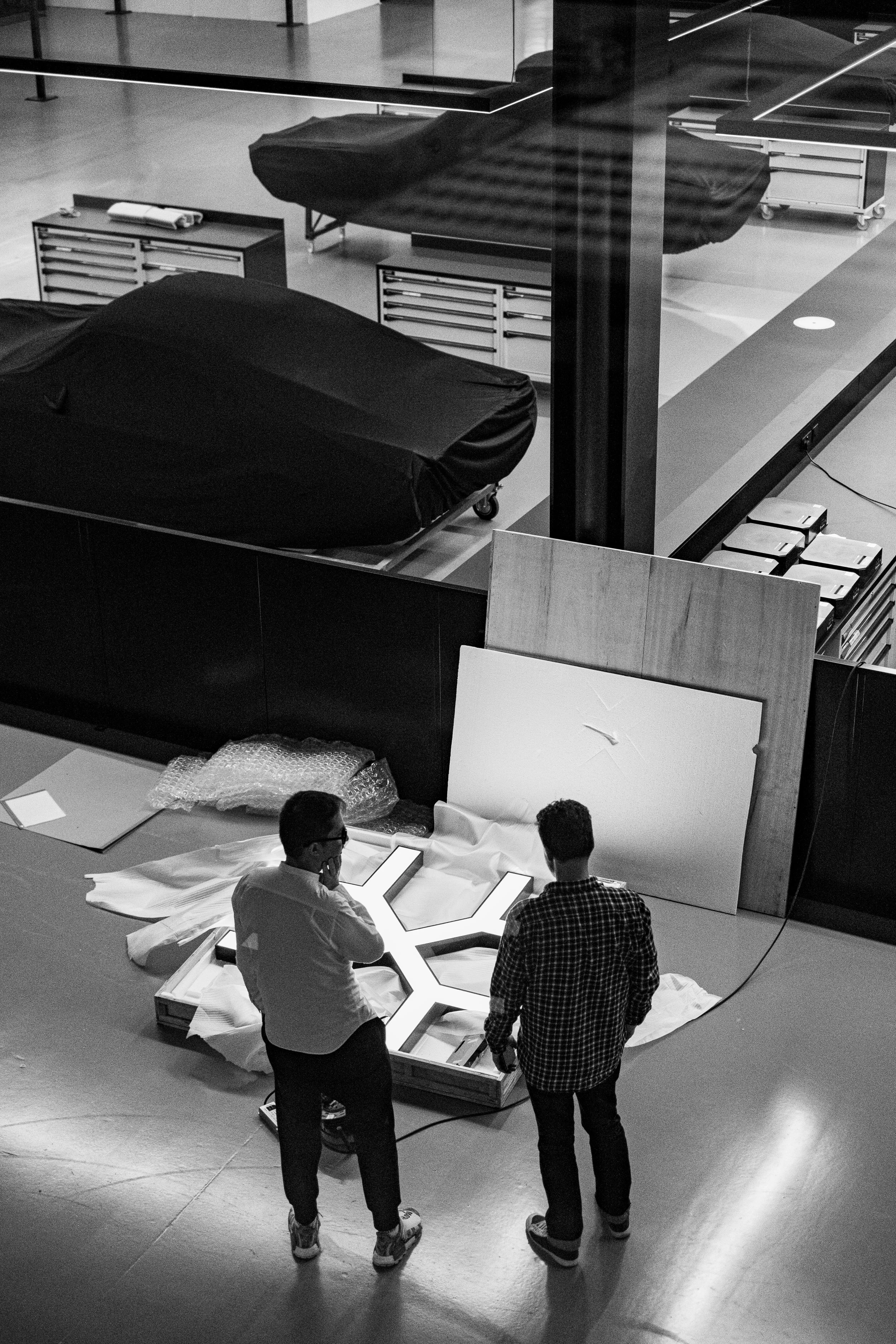

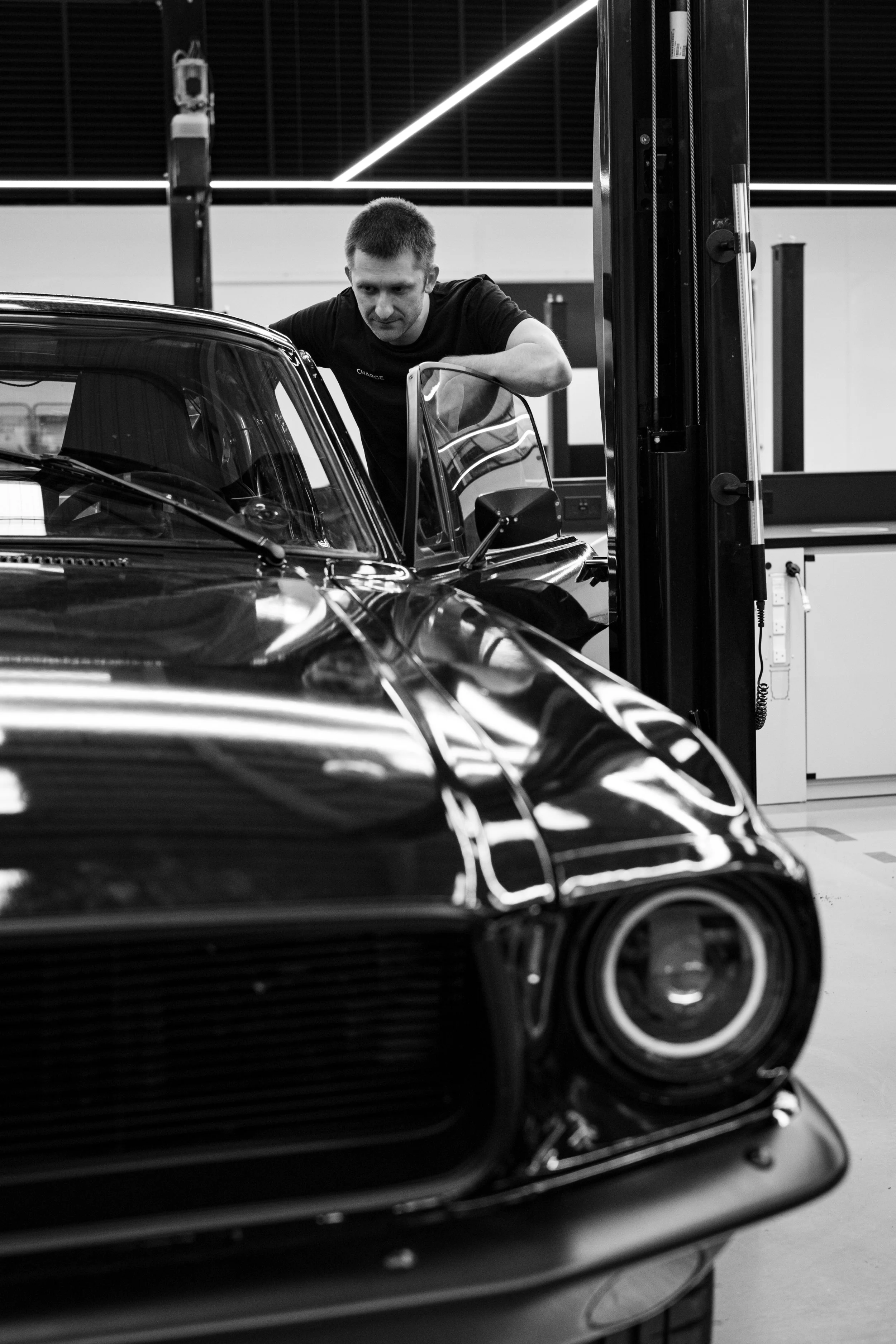

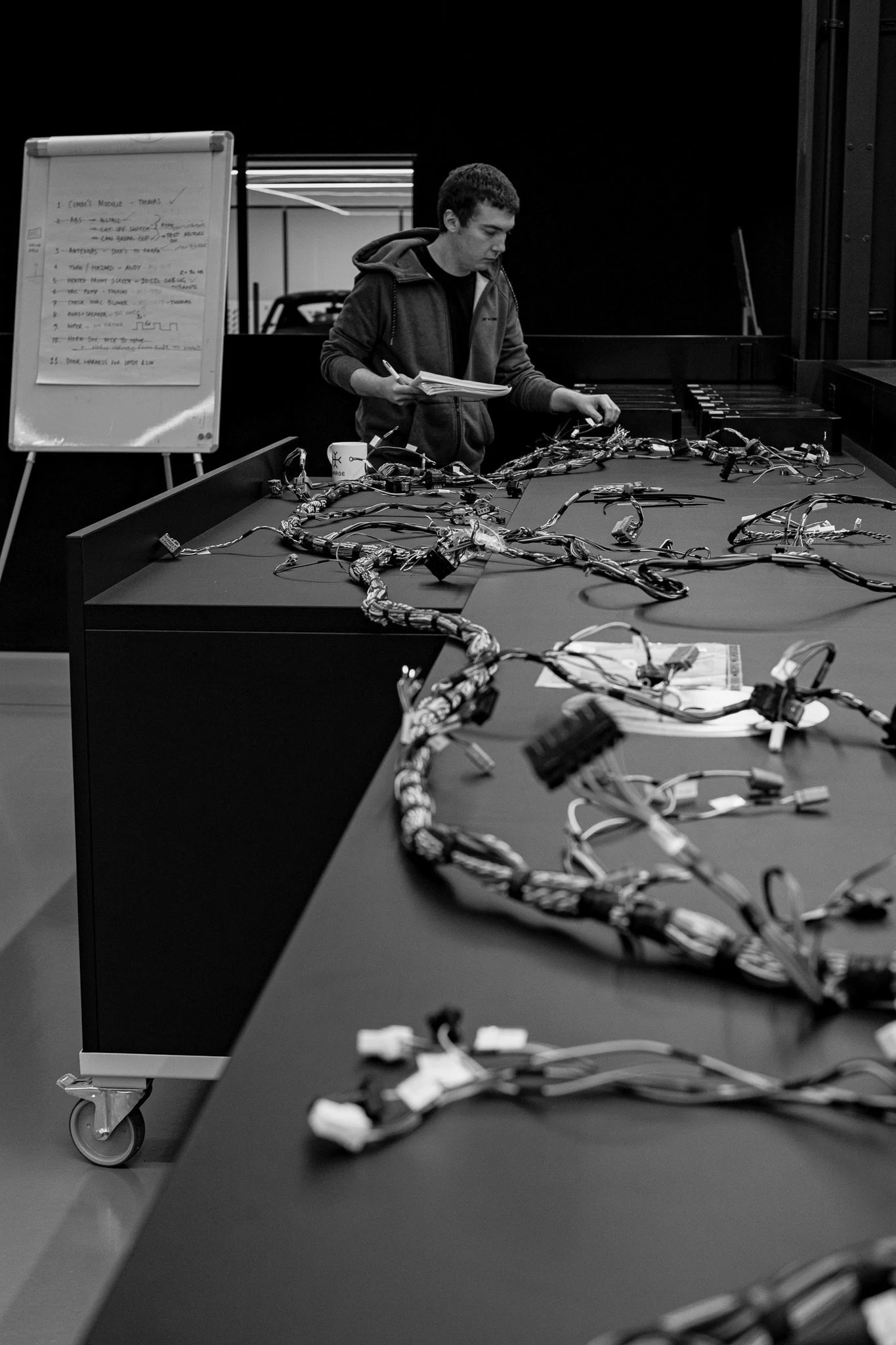


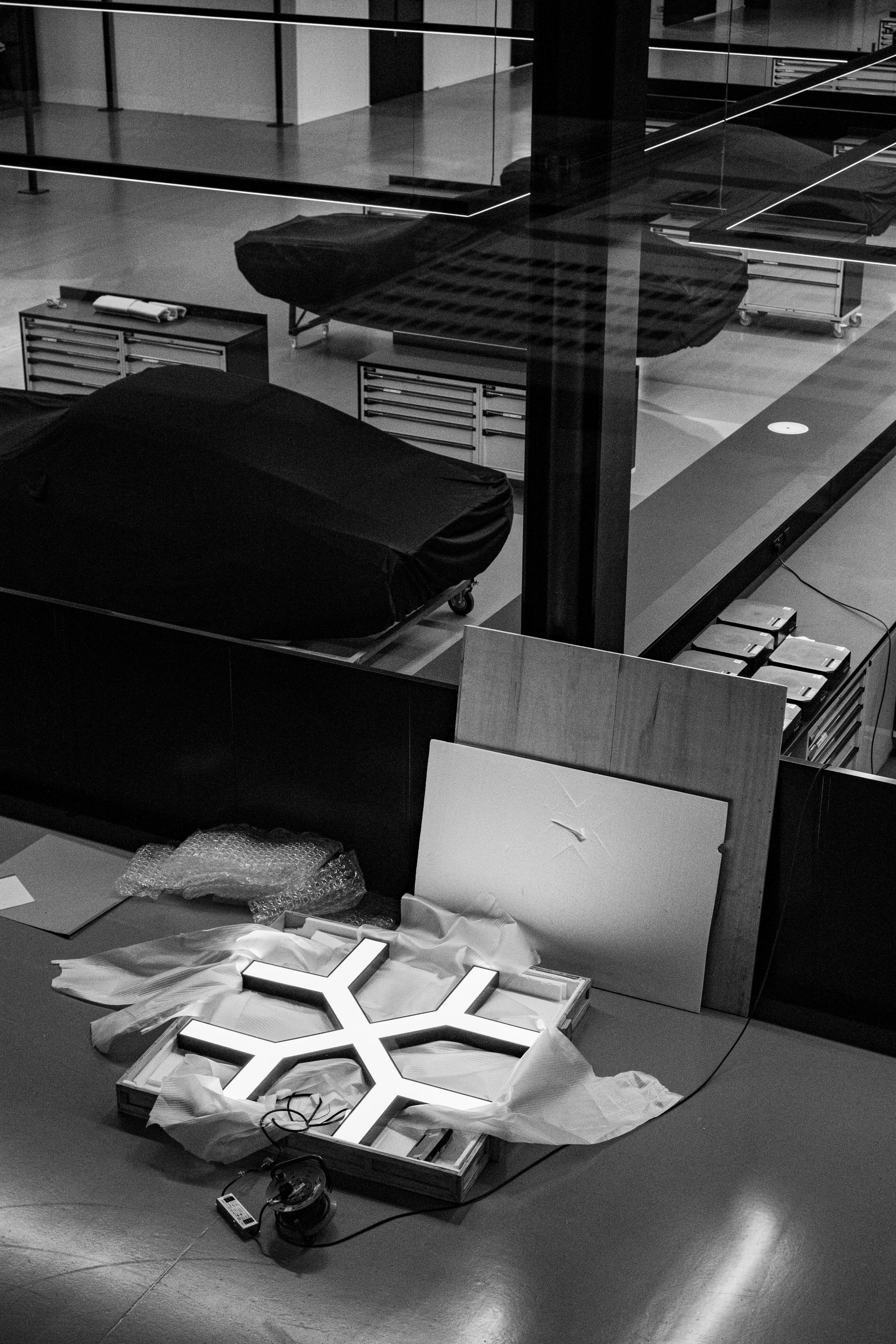
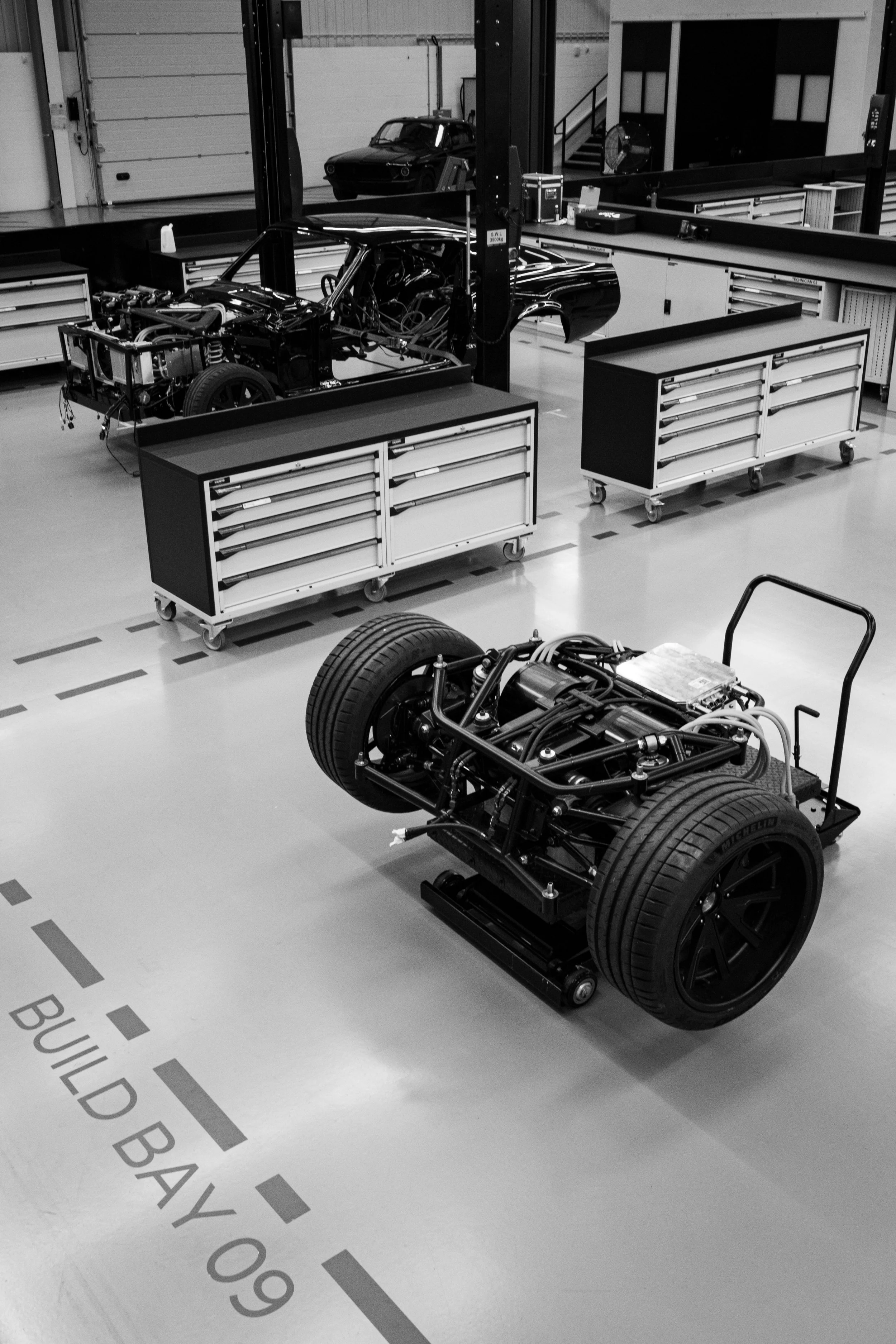
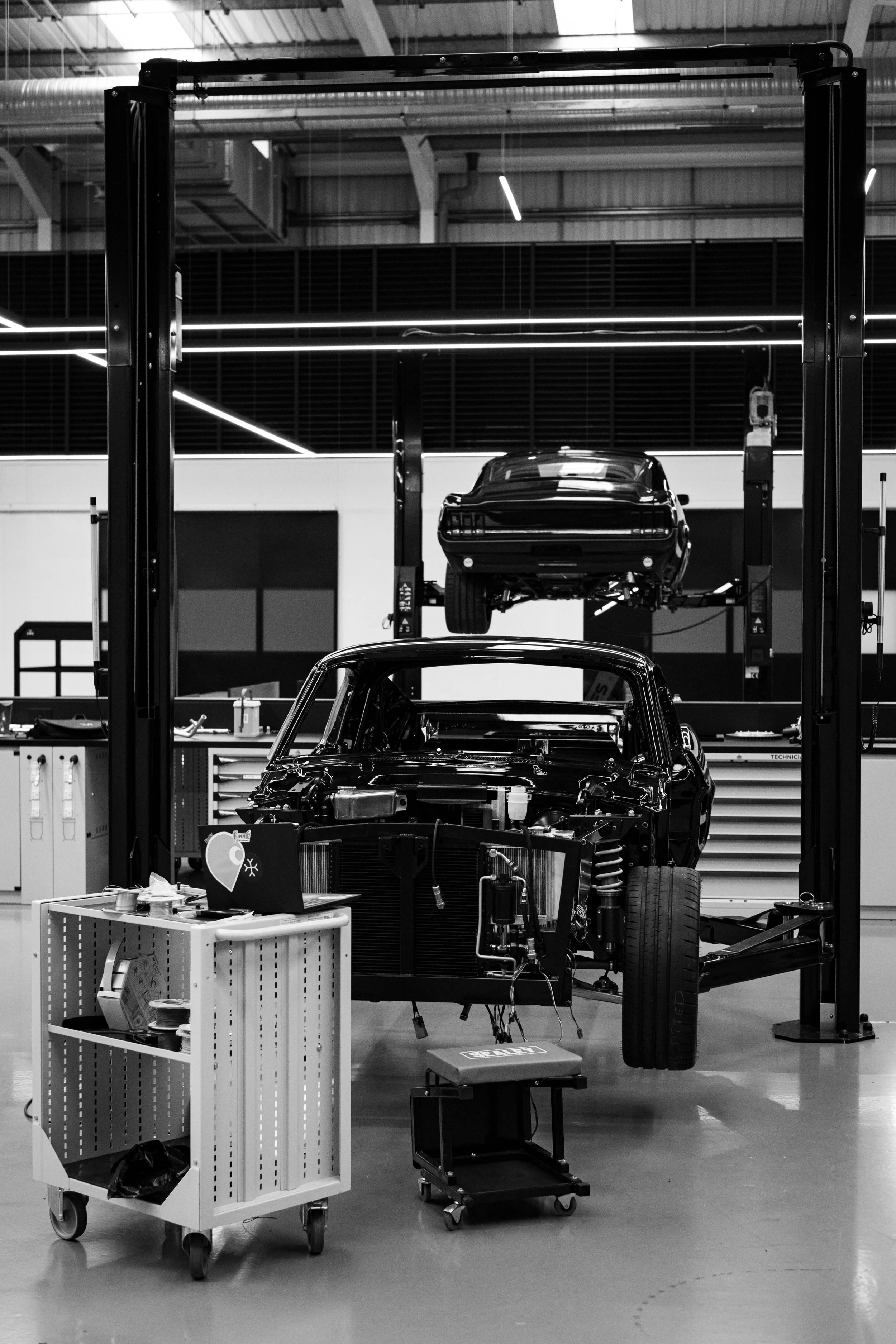

Pictured above and below:
Throughout the interior design process, VR headsets alongside real time rendering software were used to represent the final aesthetics of the interior. The VR interior was used alongside an ergonomic buck - which allows the user to interact with the controls and interior.
As the design becomes finalised, a more intricate and accurate ergonomic buck can be created, this allows the design team to do any final checks on the ergonomics and aesthetics. The buck and VR interior will be used by the clients to customise their interior in real time, so they can visualise the different colours, materials and finishes their car could have.
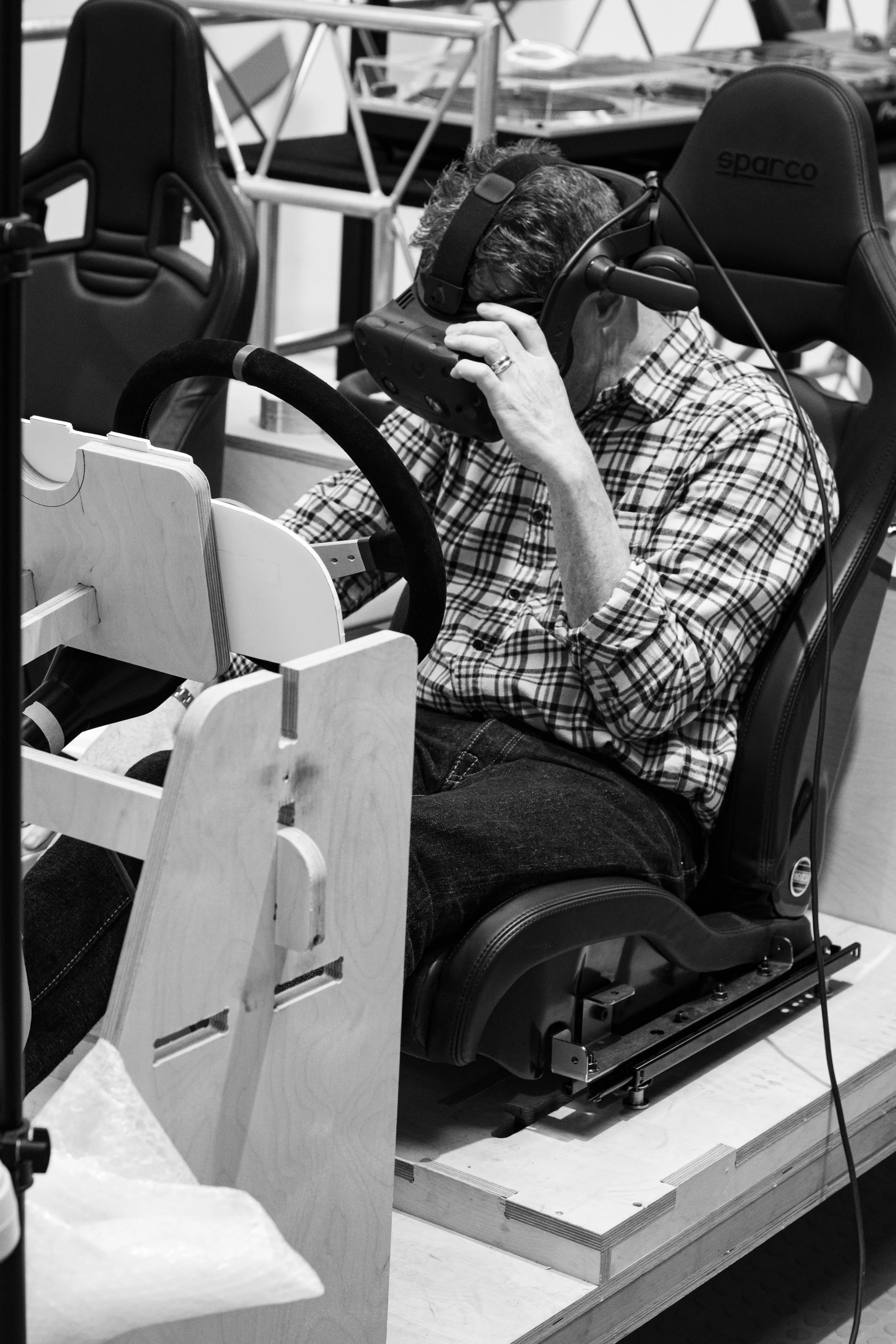
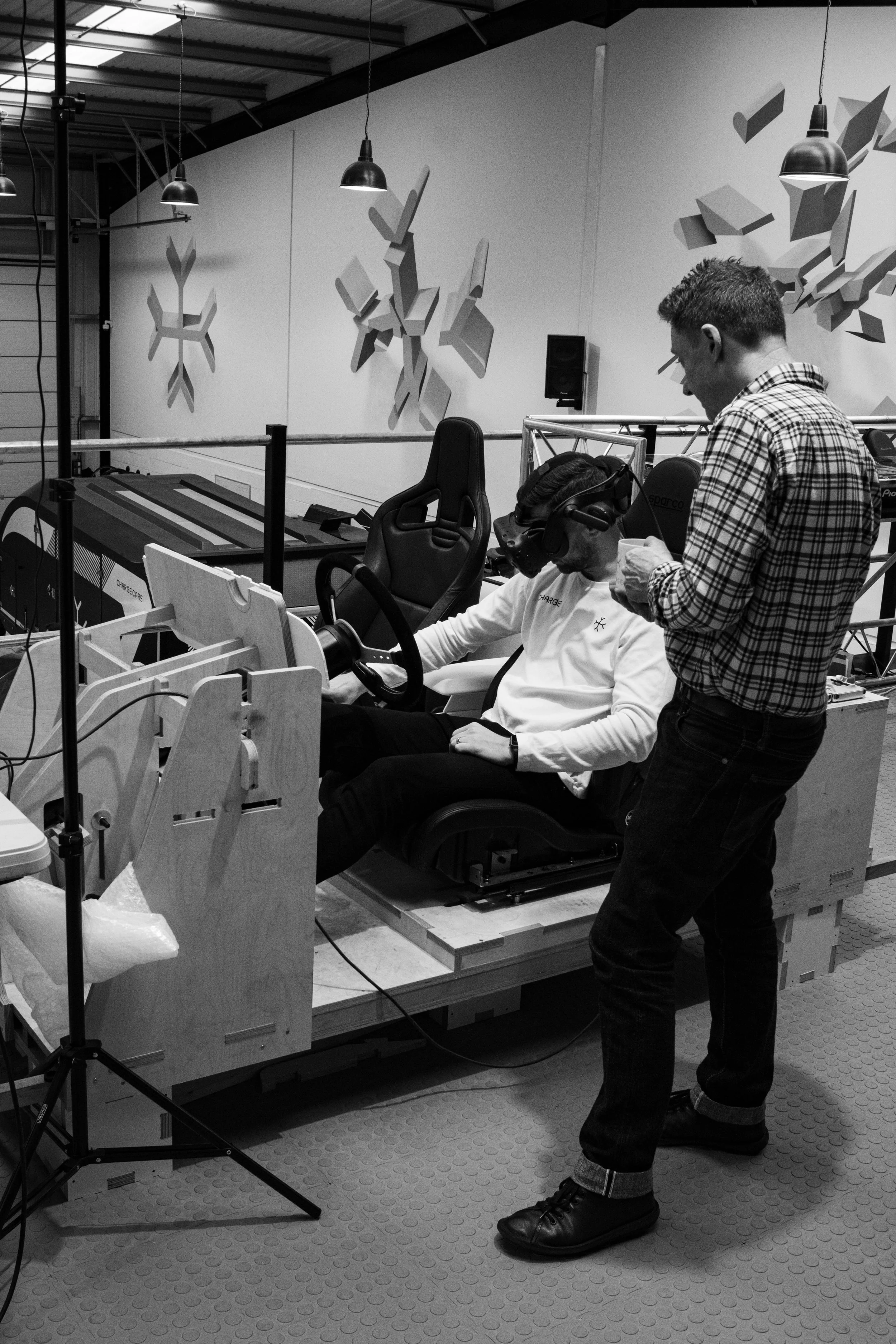
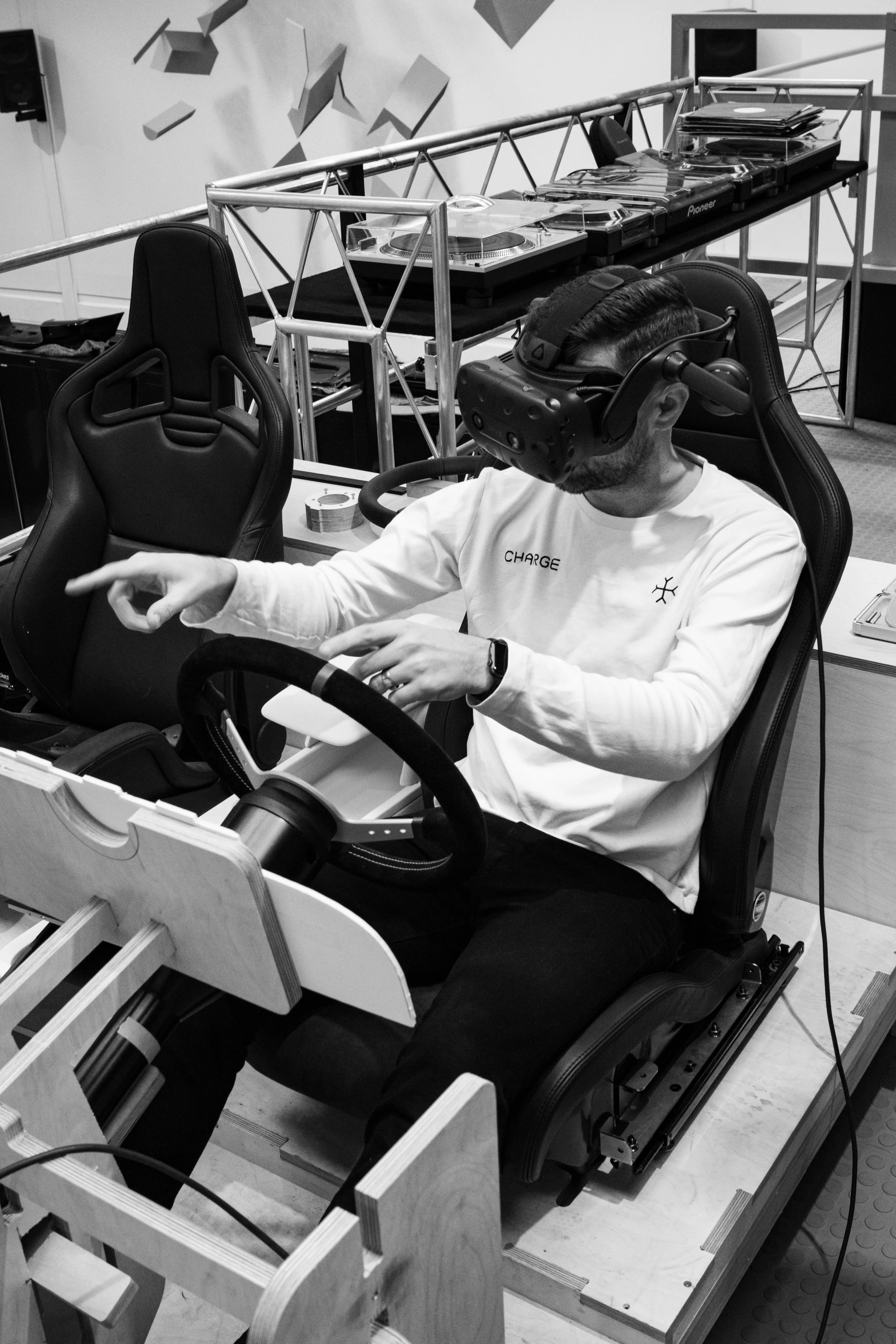

Pictured above:
3D scanning the ergonomic buck with an ergonomic dummy in the drivers seat allows the team to analyse the seating position of different people, and their ability to reach the controls. The data can also be used to set up a dummy in a crash test software.
Pictured below:
The original Mustang’s body panels were metal, Charge’s Mustang has carbon fibre body panels to reduce weight. To check the lines and panel gaps of the newly modelled panels, a full size body panel prototype was created to visualise the final asethetics.

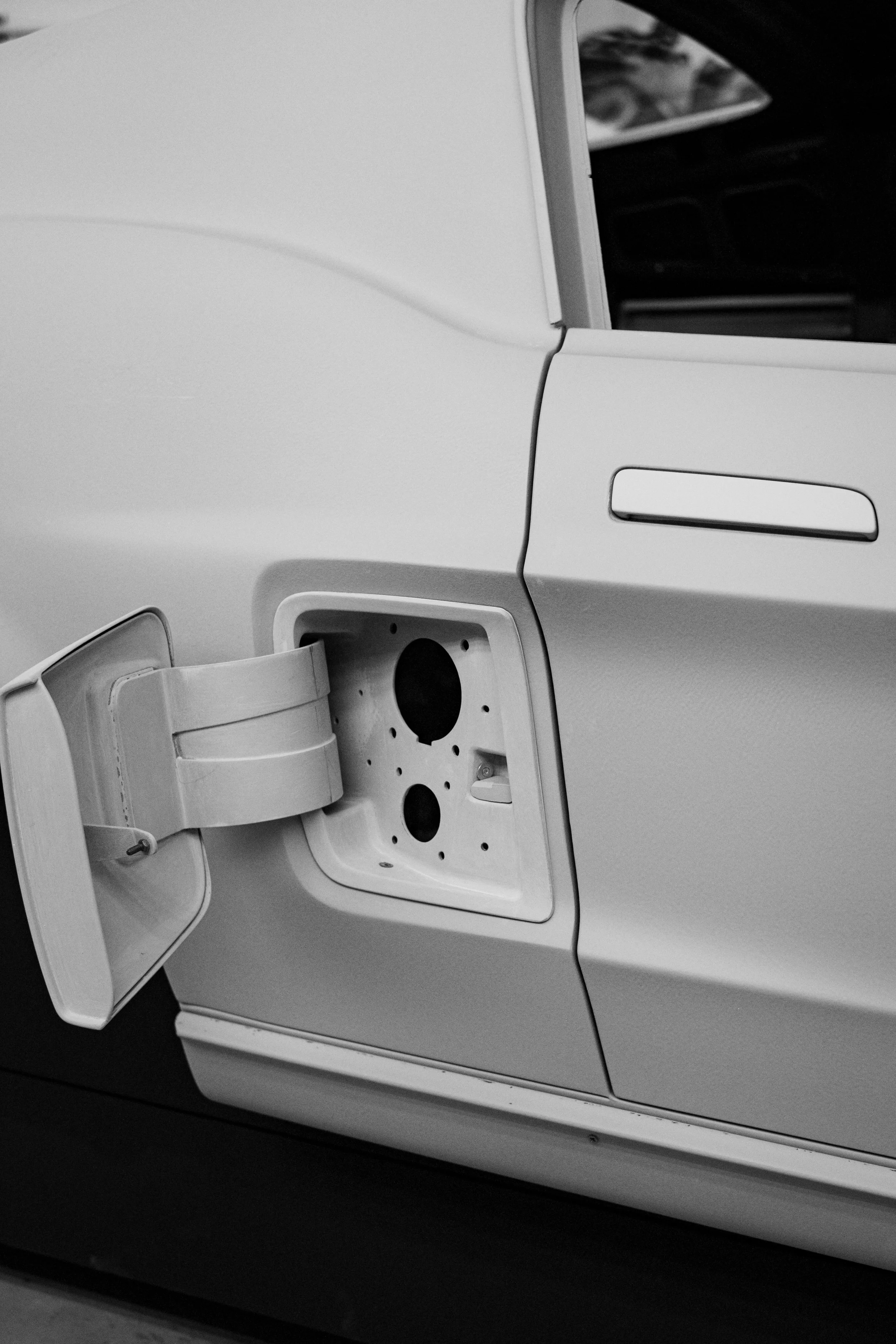
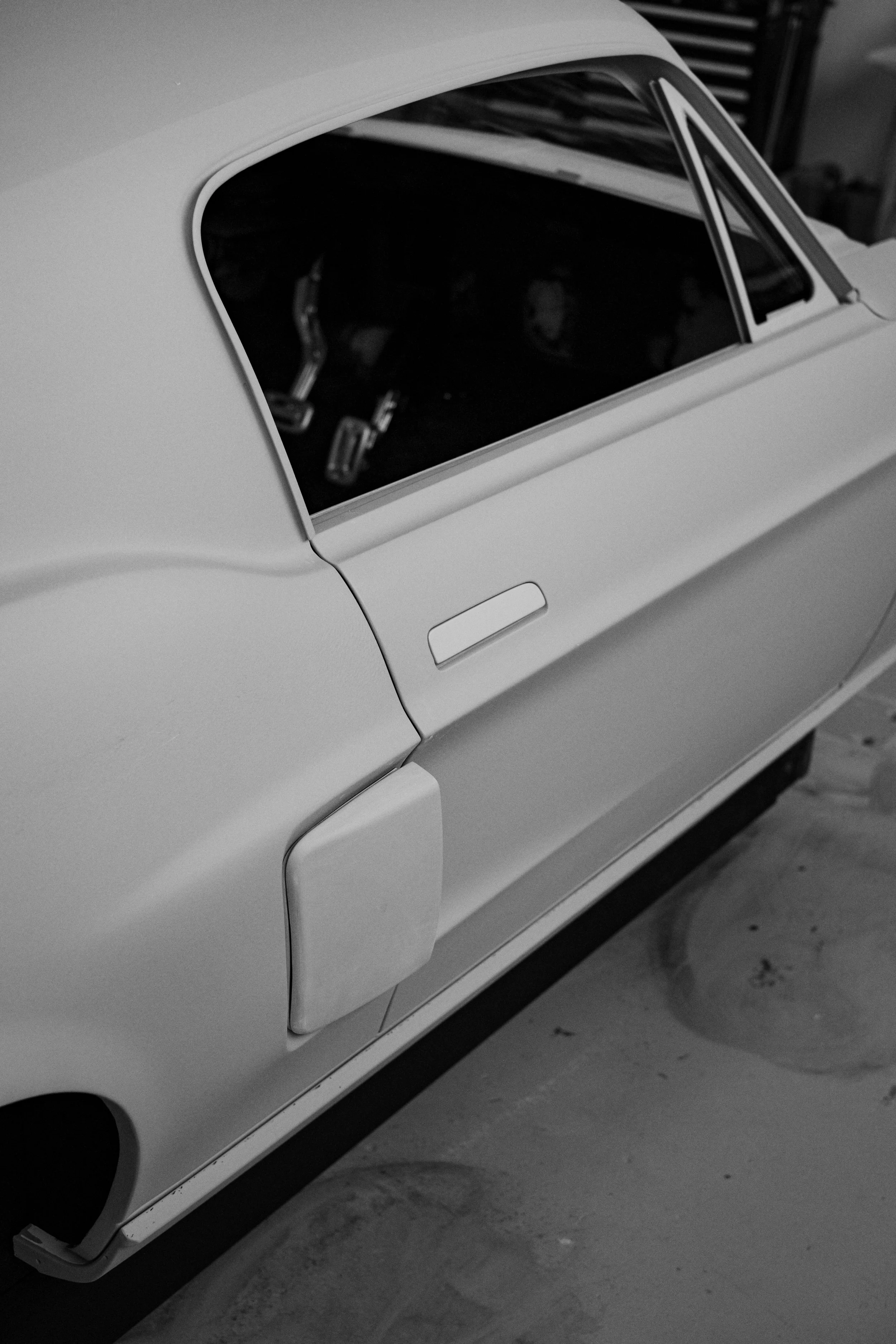

Pictured below:
During my time at Charge, there were a few video shoots, that I helped with and shot behind the scenes. There was also a few publicity shoots such as the Christmas tree on the roof of the car.
Pictured above and below:
The colour, material and finish is a very important aspect of any product, especially with custom cars, as every aspect from exterior paint to stich pattern is customisable.
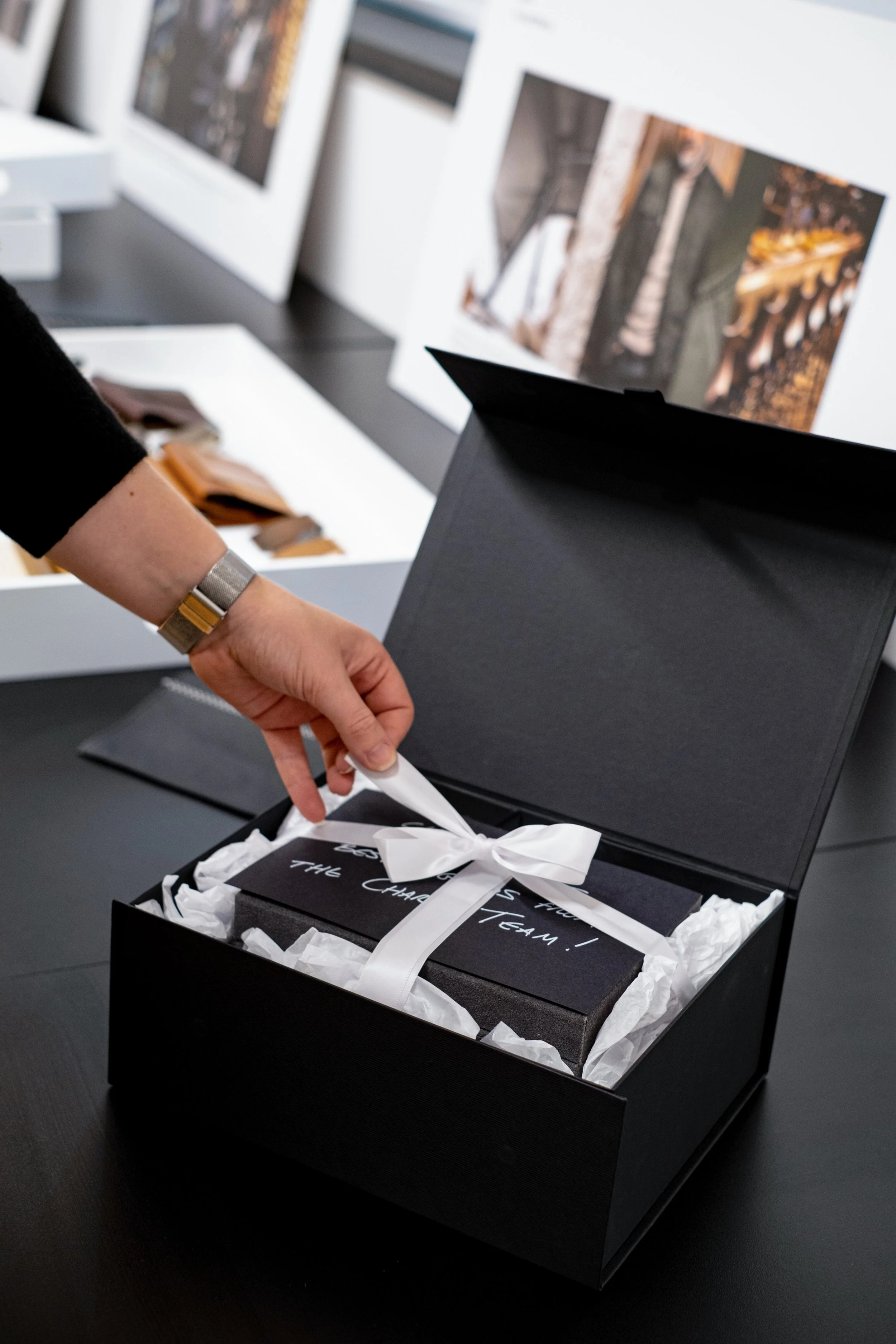
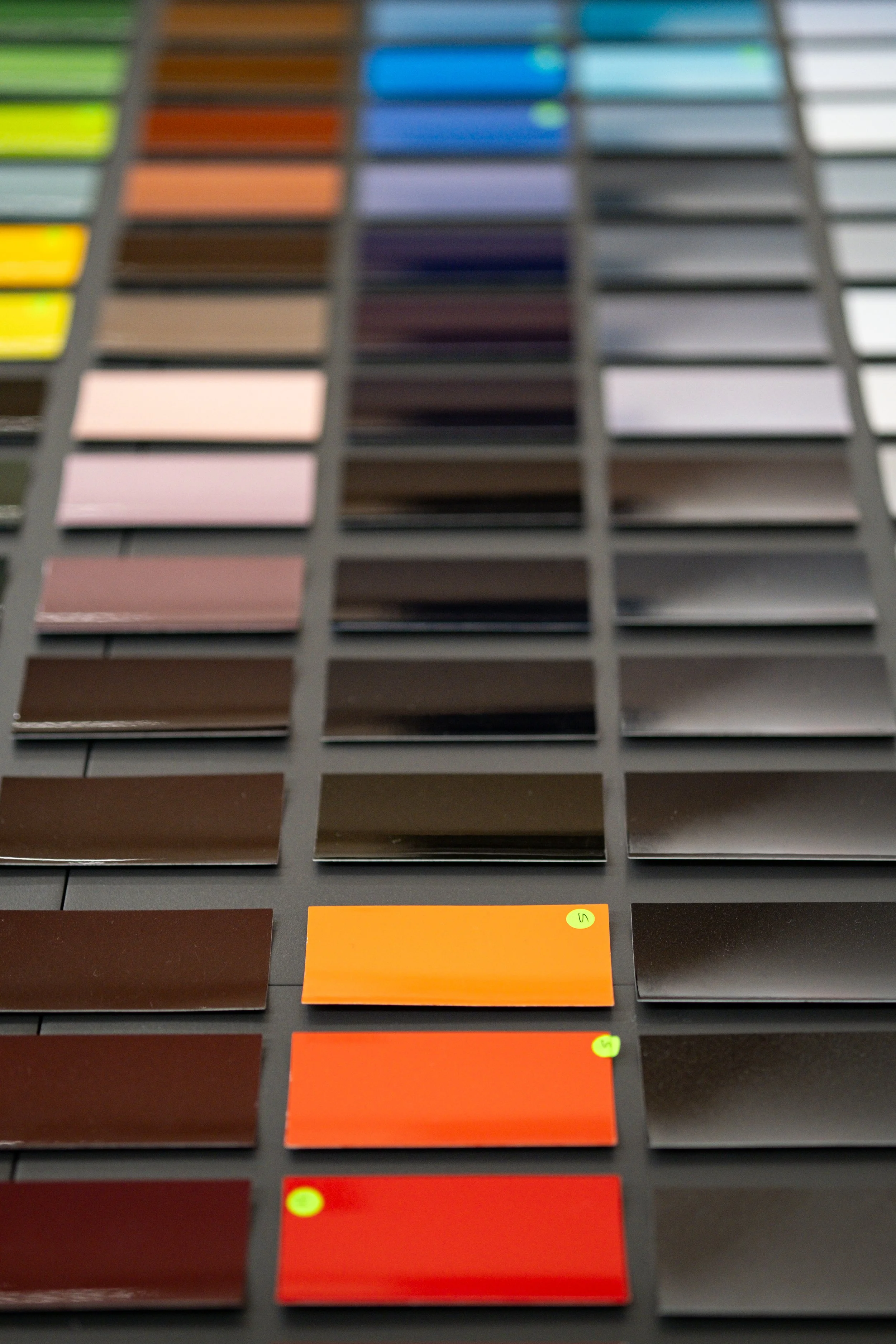
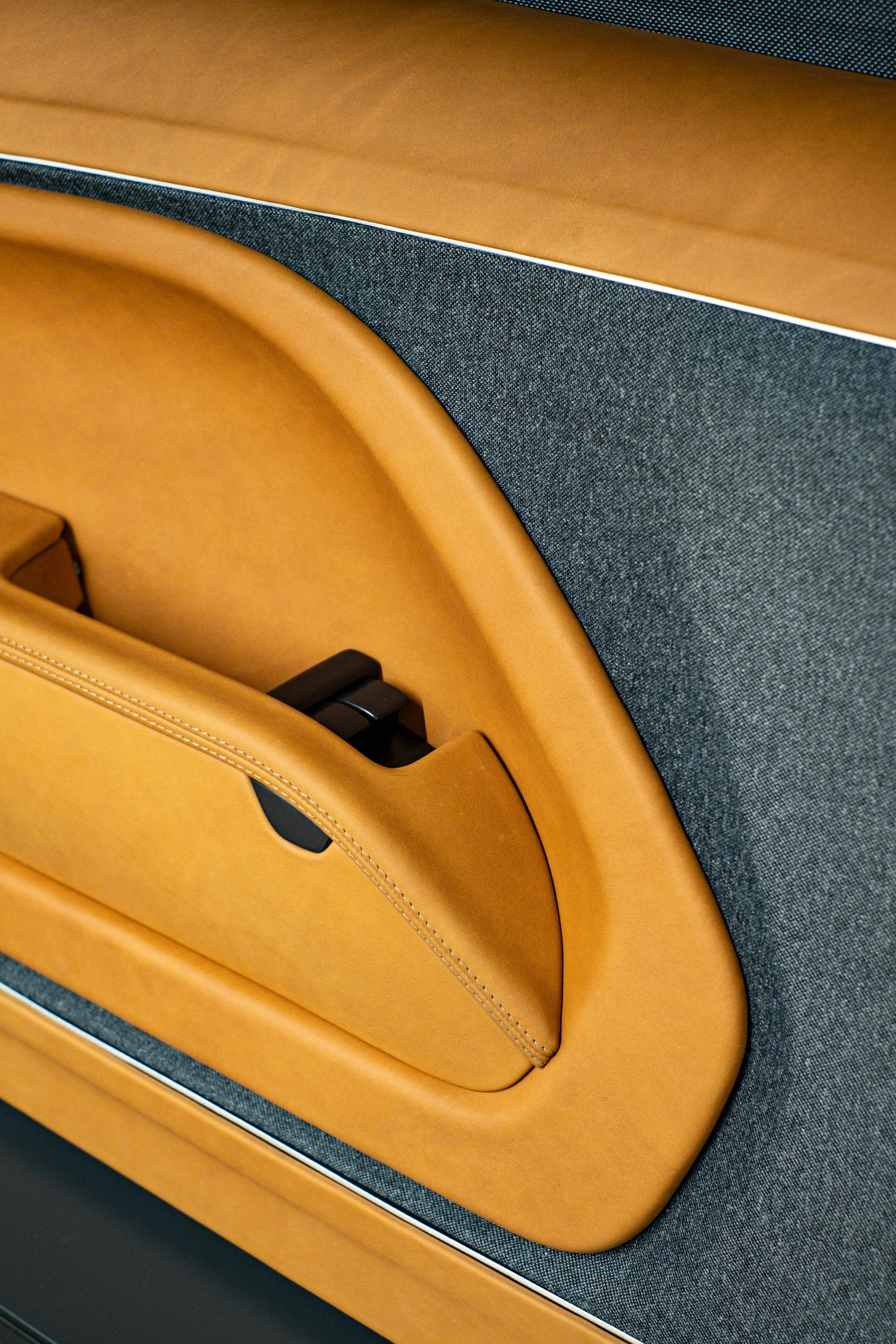
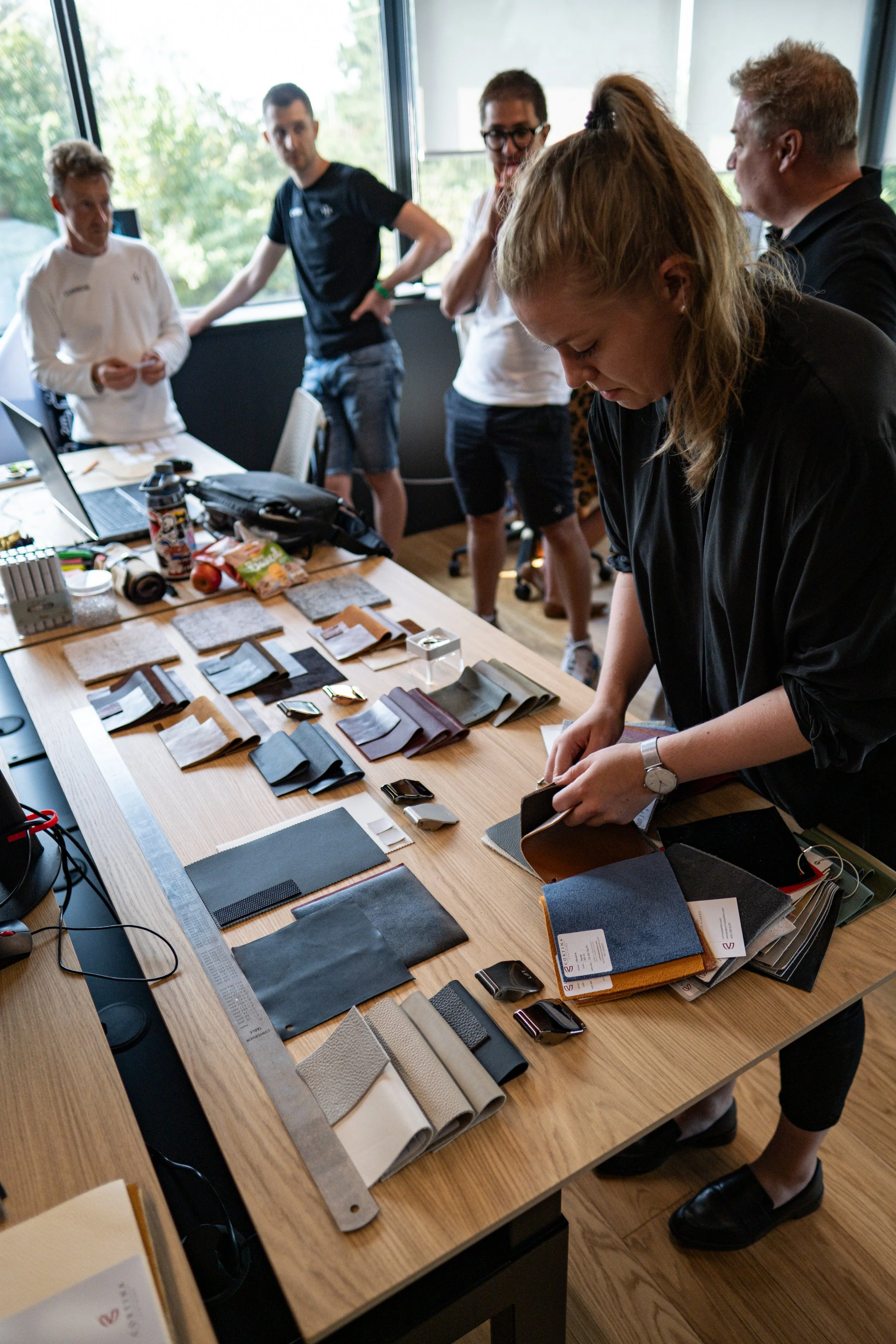